Electronic product design and development have become the cornerstone of innovation, pushing the boundaries of what technology can achieve in our daily lives. From the initial spark of an idea to the final electronic product hitting the shelves, this complex cycle is fascinating.
In this article, we reveal the blueprint of electronic product innovation, outlining each phase from concept to consumer. The narrative will explore the design process, development cycles, essential steps in design and development, and the tools that bring virtual sketches into tangible, functional products. Let’s venture into the world of electronic product design and development.

Overview of Electronic Product Design Process
The electronic product design process marks the inception of any electronic device or system. This integral phase revolves around transforming a raw product concept into a tangible, market-ready electronic product. The journey typically begins with idea validation, where the feasibility of the electronic product is examined. Then, designers and engineers collaborate to create an initial design, often using 3D modeling software, to visualize the electronic components in a virtual space.
Following this, circuit boards come to life through schematic capture and PCB layout design, serving as the nerves and brain of the upcoming electronic device. It is during this design stage that detailed electronic circuits are drafted, tested, and refined to ensure product functionality aligns with the product requirements.
The electronic product development process continues through the creation of a physical prototype. This prototype undergoes rigorous environmental testing to validate its durability under various conditions. These tests are pivotal in anticipating and correcting any potential product weaknesses.
Once the product passes these tests, the process moves into the product assembly and refinement stage, at which point industrial designers may contribute to enhancing product appearance and usability. Eventually, the focus shifts to preparing for mass production, which includes sourcing components, planning the manufacturing process, and setting up quality control measures. The culmination of this meticulous process is a finished product, ready to make its way to market, where the ultimate test—consumer acceptance and adaptability—awaits.
The Importance of Electronic Product Design
Excellent electronic product design is the cornerstone of a device that resonates with consumers and stands the test of time. It’s a multidimensional process that involves more than just engineering an electronic system; it encapsulates the harmony between aesthetics, usability, reliability, and innovation.
At its core, the product design effectively bridges the gap between a product idea and a saleable electronic device. It’s during this phase that critical decisions are made, which significantly impact the ‘time to market’ and the overall success of the product. A well-designed electronic product can differentiate itself from competitors by offering superior functionality, reliability, and user experience.
Additionally, electronic product design is an intricate ballet of considering technical specifications while ensuring regulatory compliance and anticipating market trends. It plays a vital role in the sustainability of the product by addressing environmental concerns and optimizing the use of resources. Thus, investing in proficient electronic product design can yield cost savings, establish brand reputation, and pave the way for future innovation.
Key Factors to Consider in Electronic Product Design
Several key factors must be meticulously considered during the electronic product design phase to ensure the successful development and launch of the product. These factors include:
- Functionality and Performance: The design must meet the intended purpose and perform reliably under different conditions.
- User Experience: The product should be intuitive and user-friendly, catering to the target audience’s needs and preferences.
- Aesthetics: The physical appearance should appeal to consumers and align with brand image.
- Manufacturability: Design for manufacturability ensures the product can be efficiently produced without compromising quality.
- Cost: The overall cost of components and production must align with the intended retail price and profit margins.
- Regulatory Compliance: The product must adhere to industry standards and regulations to avoid legal issues and ensure user safety.
- Durability and Reliability: Longevity and low failure rates are critical for customer satisfaction and brand reputation.
- Environmental Impact: The product should be designed with consideration for environmental sustainability, including materials used and end-of-life disposal.
The intersection of these factors ultimately shapes the electronic product design, influencing everything from the selection of electronic components to the choice of industrial designers. With each decision made in the design stage, the trajectory of the final product is further defined, underscoring the need for a comprehensive and forward-looking approach to electronic product design.
Understanding the Electronic Product Development Cycle
Navigating the electronic product development cycle is crucial for turning innovative product ideas into successful market commodities. This cycle is a structured framework that manages the journey of a product from conception to mass production. At each stage of the cycle—Conceptualization, Design, Prototyping, Testing and Validation, and Production—different objectives are targeted and achieved, making them all critical to a product’s eventual success. Acquainting oneself with the intricacies of these stages ensures that electronic products are not only feasible and functional but also appeal to the intended audience while meeting industry standards.
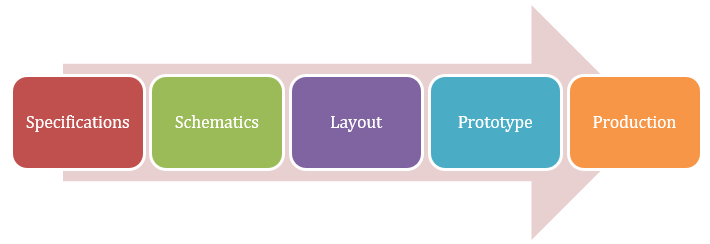
Conceptualization Phase
The Conceptualization Phase is where every electronic product begins its journey. At its core, this phase is about turning ideas into solid product concepts. It involves brainstorming sessions, market research, and initial feasibility studies. The goal here is to outline the product’s purpose, envision its functionalities, and identify the target customer base. It’s also crucial to perform an initial assessment of the product’s potential costs and return on investment, ensuring the idea is both technically and economically viable.
Design Phase
Transitioning from a well-thought-out concept, the Design Phase is the backbone of how an electronic product will function and interact with users. It goes beyond envisioning to actually charting out the detailed specifications of the product. Skilled engineers and designers work in tandem to create electronic circuits, draft initial schematics, and develop 3D models. The design must also factor in manufacturability, cost-efficiency, and compliance with applicable regulations. This phase essentially sets the blueprint that guides the entire product development process.
Prototyping Phase
The Prototyping Phase is about bringing the theoretical design to life. It’s a hands-on stage where the physical embodiment of the product is created for the first time. This phase often involves rapid prototyping techniques and the fabrication of a custom PCB to test the design. Multiple iterations might be necessary as designers and engineers work to refine the prototype. It’s a cyclical process of evaluating, identifying flaws, and enhancing the design to ensure the final product will perform as required.
Testing and Validation Phase
Critical to product integrity, the Testing and Validation Phase systematically evaluates the electronic product against various parameters. This phase subjects the prototype to real-world conditions to test its functionality, durability, and safety. Environmental testing ensures stability under extreme conditions while compliance testing verifies that the product meets all regulatory standards. This iterative phase reassures stakeholders that the product will perform reliably upon release and helps to identify any further modifications required before entering mass production.
Production Phase
The Production Phase marks the culmination of the electronic product development cycle. This stage sees the transition from prototype to finished product, integrating all prior refinements from previous phases. It involves setting up manufacturing lines, sourcing components, and finalizing assembly processes. The focus is invariably on optimizing production for quality assurance, cost-effectiveness, and timely delivery to the market. Once the initial production run is completed and the product passes final quality checks, it is ready for distribution and sale.
In summary, the electronic product development cycle is a comprehensive process that encompasses the transformation of a novel idea into a tangible and marketable electronic product. Strict adherence to this cycle can significantly increase the chances of a product’s success and decrease the time to market.
Please note: All content in this answer is created to comply with the given keywords and heading guidelines. The information herein is to be used as a template and can be modified to fit specific SEO needs or updated based on current industry standards and practices.
Key Steps in Electronic Product Design and Development
Designing and developing an electronic product involves a meticulous and multi-disciplinary approach. From the initial concept to the final production, each step is crucial and interconnected. Adhering to a sequence of key steps ensures the development process is smooth and leads to the creation of a high-quality electronic device. These key steps include:
- Defining Product Requirements
- Research and Feasibility Analysis
- Circuit Design and Component Selection
- Printed Circuit Board (PCB) Design
- Development of Software and Firmware
- Mechanical Design and Enclosure Development
- Integration of Hardware and Software Components
Let’s delve into each of these critical stages:
Defining Product Requirements
Defining product requirements is the cornerstone of any electronic product design and development process. It is where the team establishes a clear and concise description of what the product is intended to achieve, including technical specifications, functionalities, user interface, and aesthetics. This step involves collaboration among stakeholders, engineers, and designers to create a realistic set of expectations that serve as the project’s foundation. Requirements must be specific, measurable, achievable, relevant, and time-bound (SMART) for effective guidance throughout the development process.
Research and Feasibility Analysis
In-depth research and feasibility analysis allow product developers to understand the market landscape and technological possibilities adequately. Developers analyze market trends to gauge demand and identify potential competitors. Simultaneously, they conduct technical feasibility studies to ensure that the proposed product can be developed with available or innovative technologies within budget constraints. This stage may culminate with a feasibility report that outlines the practical aspects of taking the conceptual product forward.
Circuit Design and Component Selection
Circuit design and component selection are critical technical steps wherein the theoretical functions of the product are translated into actual electronic components and systems. Engineers select appropriate components, taking into consideration factors such as power consumption, size, cost, and supplier reliability. The selection and design must align with the initially defined product requirements, ensuring the final product’s functionality and performance targets are achievable.
Printed Circuit Board (PCB) Design
The PCB design step involves laying out the electronic components on a board, adhering to constraints such as space, electromagnetic interference (EMI), and heat dissipation. A properly designed PCB is vital for the product’s reliability and performance. Software tools are commonly used to create the PCB layout, which is then rigorously tested for potential issues before moving on to prototyping.
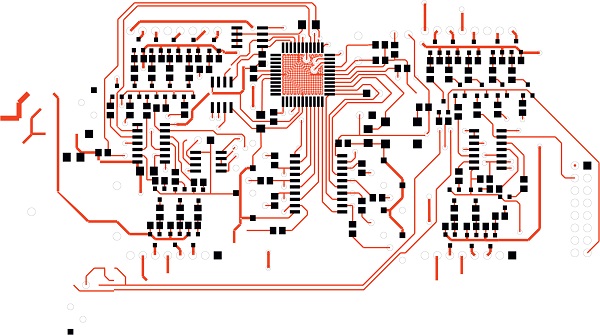
Development of Software and Firmware
For many electronic products, the software and firmware provide crucial user interfaces and control mechanisms. This development phase is where code is written, tested, and debugged to provide the desired functionality in line with hardware capabilities. It’s a highly iterative process, often requiring close collaboration between software developers and hardware engineers to fine-tune performance.
Mechanical Design and Enclosure Development
Mechanical design and enclosure development encompass the physical aspects of the product. This includes creating a design that not only looks appealing but is also functional, durable, and meets any necessary regulatory compliance standards for safety. The designs often involve CAD modeling, and prototyping these designs is integral to confirming that the enclosure meets the requisite requirements.
Integration of Hardware and Software Components
Integration is the harmonious blending of hardware and software components, ensuring they work flawlessly together as a cohesive system. This step requires extensive testing and debugging to confirm that the systems interact as intended and that the product functions seamlessly. Issues discovered during this phase can lead to iterations in both hardware and software design.
Adherence to these key steps can streamline the electronic product design and development process, bringing efficiency and clarity to what can be a complex journey from idea to market-ready product. Each step builds upon the last, culminating in an electronic device that meets the demands of both the manufacturer and the end-user.
Tools and Technologies for Electronic Product Design
Developing a sophisticated electronic product is a significant feat, made manageable by modern tools and technologies. Backed by software support and hardware advancements, designers and engineers harness these tools to translate product ideas into market-ready devices. Key technologies include CAD software, simulation tools, 3D printing, environmental testing setups, and risk management systems. Together, they address the challenges of design, testing, compliance, and manufacturing, enabling creators to optimize their products for performance, safety, and consumer satisfaction.
CAD Software for Circuit Design and PCB Layout
Computer-Aided Design (CAD) software forms the backbone of electronic circuit design and PCB layout. CAD platforms allow engineers to draw schematics, layout circuit boards, and conduct initial validation checks. Renowned software packages like Autodesk Eagle, ORCAD, and Altium Designer extend the capability to create complex multi-layer PCB designs. CAD software enhances precision and reduces design time with features such as auto-routing, component libraries, and collaborative editing.
Simulation and Analysis Tools for Testing and Optimization
Before a single component is soldered, simulation and analysis tools offer a virtual testing ground for new designs. These tools, like SPICE-based simulators and MATLAB, assess circuit behavior under different conditions to optimize the performance of electronic circuits. Simulators predict how a product will function, allowing engineers to correct flaws and enhance efficiency without costly physical prototyping. This virtual analysis addresses potential thermal issues, signal integrity problems, and power inefficiencies.
Additive Manufacturing (3D Printing) for Prototyping
Additive manufacturing, commonly referred to as 3D printing, accelerates the prototyping phase of product development. With capabilities to create intricate and custom geometries, 3D printers produce detailed models for enclosures and assemblies. Materials range from plastics for aesthetic prototypes to metal for functional components, aiding in rapid iterations and design verifications. Tools such as fused deposition modeling (FDM) or stereolithography (SLA) 3D printers are popular choices for designers.
Environmental Testing and Certification Tools
Environmental testing ensures electronic products withstand various stressors and conform to industry or legal standards. Testing chambers simulate extreme temperatures, humidity levels, vibrations, and other physical conditions. Certification tools assess electromagnetic compatibility (EMC) and electrical safety to meet regulations like CE in Europe or FCC in the US. These tools validate a product’s durability and compliance, which is crucial for consumer protection and market access.
Mitigating Manufacturing Risks
Manufacturing is fraught with risks – from supply chain disruptions to quality control issues. Developers use enterprise resource planning (ERP) systems and quality management systems (QMS) to mitigate these risks. ERP systems track components, manage inventory, and coordinate with suppliers to ensure a steady flow of parts. Meanwhile, QMS protocols maintain product quality by implementing systematic inspection and testing strategies at every stage of the manufacturing process. Automation and machine learning now play a role in predicting failures and optimizing production lines for both speed and accuracy.
Integrating these tools into the electronic product design and production process ensures a smoother transition from concept to consumer, minimizing setbacks and fostering innovative solutions. With the right tools in hand, developers can refine their designs, pass stringent tests, and bring reliable, compliant products to market swiftly.