In a world increasingly driven by technology, the demand for electronic products continues to soar, putting significant pressure on manufacturers to deliver efficiently and cost-effectively. The cost of electronic manufacturing is shaped by complex and multifaceted factors, demanding a comprehensive understanding to navigate successfully. Electronic manufacturing involves intricate processes and substantial investments, from managing inventory and shipping logistics to maintaining rigorous quality control and meeting regulatory requirements.
Understanding the economics behind electronic manufacturing begins with dissecting key expense areas, such as inventory costs, utility expenses, and quality assurance efforts. Additionally, startup ventures face considerable initial investments, including equipment purchases and workforce training, necessary to establish a foothold in the competitive market. Identifying and optimizing these cost components allows businesses to adopt advanced technologies, improve supply chain negotiations, and ultimately reduce operational expenditures.
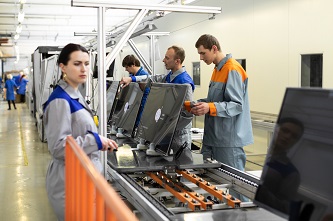
Armed with insights into the manufacturing process, from PCB design to final assembly, businesses can make informed cost decisions influenced by material choices, production volumes, and market demands. As companies grapple with fixed versus variable costs, navigating potential challenges like supply chain disruptions and regulatory compliance becomes paramount. This article delves into all these aspects, offering a detailed exploration of the cost dynamics in electronic manufacturing, providing stakeholders with the knowledge required to make informed financial strategies in this ever-evolving industry.
Key Expense Categories in Electronic Manufacturing
Electronic manufacturing involves several key expenses that can affect the final cost of a product. From purchasing raw materials to delivering a finished product to potential customers, manufacturers must manage a complex web of costs. These expenses are critical components of bringing an electronic device to market. By understanding these cost elements, companies can better manage their profit margins and customer satisfaction. Below, we will explore inventory management, shipping and logistics, utility and overhead, and quality control and testing costs.
Inventory Management Costs
Managing inventory efficiently is crucial for any electronic manufacturer. Inventory costs include the price of storing raw materials and finished goods. Warehousing costs also contribute significantly to these expenses. Efficient supply chain management can reduce inventory costs by ensuring that electronic components and raw materials are available when needed. This helps avoid delays and reduces the risk of shortages, which can lead to additional costs. Proper management ensures that companies maintain an adequate supply of critical components without overstocking, which ties up capital and increases costs.
Shipping and Logistics Expenses
Shipping and logistics are vital for delivering electronic hardware products to markets across the globe. These expenses include the cost of transporting raw materials to the manufacturing site and delivering finished products to potential customers. Shipping costs can vary based on the product category and destination. Manufacturers often look for ways to reduce these costs through efficient logistics planning and bulk shipping strategies. By optimizing routes and choosing reliable carriers, companies can lower expenses and improve their profit margins. Efficient logistics are key to minimizing delivery times and enhancing customer satisfaction.
Utility and Overhead Expenses
Utility and overhead costs encompass a range of expenses necessary to keep manufacturing operations running. Utility costs include electricity, water, and gas needed for production processes. Overhead costs cover expenses like rent, salaries for non-production staff, and administrative expenses. Managing these costs effectively ensures that they do not eat into the company’s profit margin. Manufacturers can reduce utility expenses by implementing energy-efficient technologies and practices. Overhead costs can be managed through better planning and by streamlining administrative processes. Keeping these costs in check helps maintain product quality and market competitiveness.
Quality Control and Testing Costs
Quality control and testing are essential to ensure product reliability and customer satisfaction. Testing costs arise from the need to inspect electronic devices for defects before they reach the market. This process can involve expensive equipment and specialized personnel. Product quality is crucial for maintaining a good reputation and reducing returns, which can incur additional costs. Standard pricing for these activities depends on the complexity and larger volume of production. By investing in effective quality control and testing, companies can minimize the risk of product defects and improve overall reliability. This investment not only enhances customer satisfaction but also protects the company’s reputation in the competitive electronic products market.
Startup Costs for Electronic Manufacturing Companies
Starting an electronic manufacturing company can be an exciting venture, yet it requires significant investment. Understanding the various startup costs gives insight into financial planning. Manufacturing costs range from machinery to labor, raw materials to workforce training. Each aspect impacts the overall budget and business longevity. Recognizing these costs is crucial for potential success and profitability. As you consider entering the electronic industry, balancing these expenses with expected profits will guide your company’s growth and stability.
Machinery and Equipment Purchase
Purchasing machinery and equipment is a primary cost for electronic manufacturing businesses. This step involves acquiring tools and machines necessary to produce electronic products effectively. These machines may include assembly lines, soldering equipment, and testing devices. Investing in high-quality, reliable equipment is vital for achieving product quality and customer satisfaction. While the initial purchase can be expensive, buying the right equipment ensures efficiency and helps prevent production defects. Ensure to consider additional costs like installation and maintenance, as these are critical components of the overall manufacturing costs.
Raw Materials Acquisition
Acquiring raw materials is essential for producing electronic components and completed devices. These materials can include semiconductors, metals, and plastics. The cost of raw materials affects both the cost per unit and the final product price. A robust supply chain management strategy is necessary to secure quality materials at the best standard price. Fluctuations in raw material prices can impact profit margins and production costs, requiring careful inventory management. Negotiating with suppliers and purchasing in larger volumes may provide cost advantages. Ensuring a consistent supply of raw materials is key to maintaining production process continuity and product to market reliability.
Initial Training and Workforce Development
Training and developing a skilled workforce is crucial for successful electronic manufacturing. Initial training programs ensure staff are equipped to handle advanced machinery and production techniques. The focus should be on improving product quality and reducing product defects. Developing a competent team also enhances product reliability, directly affecting customer satisfaction and potential customers’ trust. The labor cost associated with training can be significant, but investing in workers’ skills can result in improved production efficiency. A well-trained workforce helps maintain quality standards, ultimately leading to better profitability and a more robust market position.
Reducing Operational Costs
Reducing operational costs in electronic manufacturing is vital for maintaining a healthy profit margin. By cutting unnecessary expenses, manufacturers can offer electronic products at competitive prices. A focus on efficiency helps in lowering production costs and improving product quality. However, reducing costs shouldn’t compromise on key areas like product reliability and customer satisfaction. Effective strategies in inventory, supplier management, and technology adoption can lead to a significant decrease in overall costs. Below are some ways to achieve these savings and ensure your finished product remains favorable in the market.
Optimizing Inventory Management
Optimizing inventory management is crucial for reducing operational costs. Efficient inventory systems help monitor electronic components and raw materials, leading to lower inventory costs. With better tracking, companies can reduce excess stock and minimize warehousing cost. This ensures that electronic hardware products are readily available to meet production demand without incurring additional costs. Predictive analyses and demand forecasting help in making informed decisions to balance inventory levels. These practices contribute to smoother supply chain management and higher profitability.
Negotiating Supplier Contracts
Negotiating supplier contracts effectively can contribute to cost savings. Manufacturers aim to secure better deals on critical components and raw materials. Strong negotiation skills can lead to favorable terms and lower prices, impacting the production cost per unit positively. Establishing long-term relationships with suppliers also helps in securing stable prices for larger volume orders. Besides, collaboration with suppliers can enhance product quality and reduce the chances of product defects, ensuring better customer satisfaction.
Adopting Advanced Technology
Adopting advanced technology can be a game changer in lowering manufacturing costs. Automation and AI in the production process enhance productivity and improve product to market speeds. By implementing robotics and smart technology, assembly costs can be minimized. Investments in technology can lead to fewer product defects and improved product reliability. Additionally, real-time tracking software aids in efficient supply chain management. Though initial costs may be high, the long-term benefits outweigh the expenses and lead to substantial savings.
Streamlining Marketing Strategies
Streamlining marketing strategies can significantly cut down on overhead costs. Focusing marketing efforts on the right product category and potential customers ensures a higher return on investment. Leveraging digital marketing platforms can be more cost-effective than traditional methods. Analyzing market trends and customer preferences helps tailor messages that resonate well with the target audience. By optimizing marketing campaigns, companies can boost product awareness while taking full advantage of the standard price models to drive sales efficiently.
Understanding the Manufacturing Process
Understanding the electronic manufacturing process is key in controlling costs and ensuring product quality. The process begins with designing a product, which includes choosing the right electronic components. Each component must meet specific quality standards to ensure product reliability. After the design phase, prototyping helps identify potential issues before full-scale production. The production process involves assembly and ensures the finished product meets customer expectations. Critical components must be strategically sourced to maintain a healthy profit margin. Efficient supply chain management is essential in controlling costs, from raw materials to labor. By understanding these aspects, businesses can deliver electronic hardware products to the market more effectively.
PCB Design Costs
Printed Circuit Boards (PCBs) are crucial in electronic devices. PCB design costs depend on several factors, including size, complexity, and the number of layers required. Multi-cavity molds and other advanced features can raise costs but may be necessary for the product category. The standard price for PCB design varies, but higher costs often ensure better product quality and reliability. It’s important to factor in potential customizations or critical components that may drive up the cost. The goal is to balance between budget and quality while ensuring the design supports the intended product features. Effective design can lead to lower production costs and higher customer satisfaction.
Prototyping Expenses
Prototyping is an essential step in the development of electronic products. It involves creating a working model to test the design and functionality. The costs for prototyping can vary based on the complexity of the electronic device. A larger volume of prototypes may help in identifying product defects early and refine the design to prevent defects in the finished product. The benefit of investing in prototyping is avoiding costly errors during mass production. Understanding these expenses is crucial for maintaining a profit margin and ensuring a reliable product. Though it may seem like an additional cost, prototyping plays a key role in achieving product to market readiness.
Assembly and Production Costs
Assembly and production are significant parts of the manufacturing process. These costs include labor cost, overhead costs, and equipment expenses. Labor cost can vary based on the region and the skill level required for product assembly. Efficient assembly ensures timely delivery and impacts warehousing cost and shipping cost. Raw materials and inventory costs must be managed to keep production costs in check. Assembly costs can be reduced through process optimization and strategic planning. By considering all factors, businesses can improve product reliability and customer satisfaction. Effective control of assembly and production costs is vital for maintaining a competitive edge in the market.
Factors Influencing Cost Decisions
In electronic manufacturing, cost decisions are influenced by a variety of factors. These include the cost of materials, labor, and overheads. Production costs can rise due to fluctuations in raw material prices or labor rates. Additional costs can stem from shipping, warehousing, and inventory management. Supply chain management plays a crucial role, as delays can affect delivery schedules and increase costs. Also, the choice of technology and manufacturing process impacts the cost. Efficient processes can lower expenses and increase profit margins. Assessing these costs allows manufacturers to set a standard price for their products. It’s important for companies to consider these factors to maintain product quality and meet customer demands cost-effectively.
Material Selection and Sourcing
The choice of materials is vital in electronic manufacturing. Selecting high-quality electronic components can ensure product reliability. However, raw materials with higher quality often cost more. Sourcing these materials requires strategic planning. Efficient supply chain management can help in acquiring critical components at competitive prices. Additionally, the location of suppliers affects shipping costs. Companies often balance quality with cost to maintain competitive pricing. By doing so, they can maximize their profit margins while ensuring customer satisfaction. It’s crucial to keep additional costs, such as import taxes, in check to achieve cost-effective production.
Production Volume Impact
The volume of production significantly affects manufacturing costs. Producing electronic products in larger volumes often reduces the cost per unit. This is due to economies of scale, where overhead costs, such as warehousing and assembly expenses, are spread over more units. When companies order in bulk, they can negotiate better prices for electronic components. However, a larger volume may also require a more significant initial investment and careful inventory management. Multi-cavity molds can speed up production, balancing costs with efficiency. Calculating the optimal production volume is essential to maintain a healthy profit margin and ensure product to market readiness.
Timeline and Speed of Production
The speed and timeline of production also influence costs. Faster production can lead to quicker product to market processes, which is advantageous in competitive environments. However, hurried manufacturing might risk product quality and lead to defects. Timely production relies on streamlined processes and efficient management of labor costs. Similarly, reliable scheduling minimizes additional costs from delays. Companies need to adjust the production timeline based on demand and supply chain efficiency. This balance ensures that the finished product meets market expectations without incurring excessive costs. Meeting tight deadlines without compromising on quality can enhance customer satisfaction and attract potential customers.
Fixed vs. Variable Costs in Manufacturing
In the world of electronic manufacturing, understanding the cost structure is vital for financial planning and strategy. Production costs are mainly divided into fixed and variable expenses. Grasping the difference between these two types is crucial for predicting costs and setting a competitive standard price. Fixed costs remain constant regardless of production volume, while variable costs change with the production level. Balancing these is essential in managing profit margins and customer satisfaction. By optimizing both types, businesses can maximize efficiency and reduce overhead costs, ultimately enhancing product quality and product reliability.
Defining Fixed Costs in Electronics Manufacturing
Fixed costs in electronics manufacturing are expenses that do not fluctuate with production levels. These include rent for manufacturing facilities, salaries for permanent staff, and maintenance equipment. These costs are predictable and remain constant, regardless of how many electronic devices or components are produced. For instance, the rent for a factory remains the same whether you manufacture ten units or a thousand. Due to their consistency, fixed costs allow for better supply chain management and planning.
Moreover, fixed costs play a huge role in manufacturing overhead costs. This consistency helps calculate the standard price for electronic products. Despite being constant, these costs need regular monitoring. A company can better understand its financial health by keeping track of these expenses. Knowing fixed costs also aids decisions regarding scaling operations and entering new product categories. In conclusion, keeping fixed costs in check ensures the company can maintain its product to market efficiently.
Identifying Variable Costs and Managing Fluctuations
Variable costs in electronics manufacturing are expenses that change with production output. These costs include raw materials, assembly costs, and labor costs. For instance, when producing electronic hardware products, the cost per unit will rise if you need more raw materials for a larger volume of finished products. This fluctuation makes variable costs harder to predict compared to fixed costs.
Managing these fluctuations involves strategic planning and effective inventory management. Companies can minimize variable costs by optimizing the use of multi-cavity molds in production. Another approach is to purchase raw materials in bulk. Larger orders often come with discounts, thereby reducing the price per component. An efficient supply chain management strategy also aids in balancing these costs.
Understanding variable costs is crucial for maintaining product quality and ensuring customer satisfaction. By keeping these under control, businesses can better handle potential customers’ demands and improve profit margins. A focus on these areas helps maintain competitive prices while reducing risks of product defects and boosting overall product reliability.
Risks and Challenges in Electronic Manufacturing
Electronic manufacturing involves several stages, each with its own potential risks and challenges. These can range from supply chain disruptions to changes in technology. Managing these challenges effectively is crucial to ensure production remains smooth and costs are kept in check. While striving for high product quality, manufacturers must also consider various production costs, such as labor, raw materials, and shipping. In a competitive market, maintaining a balance between cost-efficiency and product reliability is essential. This helps in achieving a significant profit margin and ensuring customer satisfaction.
Supply Chain Disruptions
Supply chain disruptions can dramatically affect electronic manufacturing. They occur when the delivery of critical components or raw materials is delayed. These disruptions increase inventory costs and can lead to unmet deadlines. Key causes include natural disasters, political instability, or global events. Businesses must have strong supply chain management to tackle these issues. Ensuring multiple suppliers for critical components helps mitigate risks. This aids in keeping overhead costs stable and maintains the flow of electronic products. Additionally, effective forward-planning can protect production schedules from unexpected disruptions.
Compliance and Regulatory Challenges
Adhering to compliance and regulations is vital in electronic manufacturing. These laws ensure product safety and environmental protection. Regulations affect many aspects, including product design and waste management. Non-compliance can have severe consequences, such as fines or legal action. Adapting to these regulations requires investment in knowledge and resources. Manufacturers must stay updated on any regulatory changes in different regions. This means hiring experts or consultants who understand compliance requirements. Proper documentation and certification are crucial to comply with international standards. Ensuring compliance also boosts the company’s reputation, making it more attractive to potential customers.
Technological Advancements and Adaptation
Technological advancements significantly impact the electronic manufacturing industry. Rapid changes demand that manufacturers adapt quickly to stay competitive. New technologies can reduce manufacturing costs and improve product quality. However, they require investment and training. Implementing advanced machines, like multi-cavity molds, can lead to larger volume production. But this involves analyzing the cost per unit and reassessing the product to market strategies. Keeping up with technological changes also means upgrading existing electronic hardware products. Failing to do so could result in product defects or reduced product reliability. Embracing technology ensures that electronic devices meet the standard price, keeping in line with customer expectations.