Imagine the precise care it requires to construct a puzzle, where each piece firmly affects the final image. Within the realm of manufacturing, the Bill of Materials (BOM) represents this intricate assembly, with its cost serving as the backbone of product pricing and profit margins. BOM cost determines the financial blueprint from which a product will emerge.
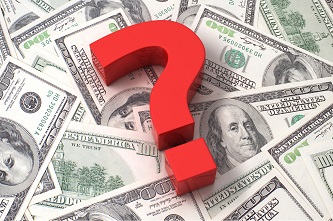
From the moment raw materials are sourced until the final product leaves the assembly line, the BOM cost encompasses all aspects, including labor, components, and indirect expenses. Its significance cannot be overstated; it is the bedrock of strategic planning and competitive pricing in the manufacturing industry.
In the forthcoming article, we delve into the complexities of BOM cost, investigating its influence on product development. We’ll explore the multifaceted factors affecting BOM cost, unravel strategies for optimization, analyze the tools for meticulous cost management, stroll through concrete case studies, and contemplate the challenges in maintaining cost efficiency amidst market volatility.
What is BOM Cost?
The term “BOM cost,” often referred to as Bill of Materials cost, is an extensive accounting of all the expenses incurred during the production of a physical product. It is an integral component of the manufacturing process, serving as a financial roadmap that illustrates the actual costs involved in transforming raw materials into a finished product. The BOM cost encompasses a wide range of cost categories, including but not limited to, the costs of materials, individual component costs, labor costs involved in the creation of the product, and other indirect expenses such as energy usage, equipment depreciation, and factory overhead.
By meticulously detailing each aspect of the expenditure, from component quantities to unit prices, a BOM provides a structured, itemized list that enables manufacturers to calculate the overall production cost with precision. This financial breakdown is crucial not only for pricing products accurately but also for identifying cost reduction opportunities within the manufacturing processes.
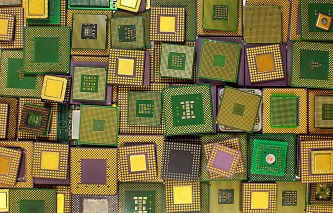
Definition of BOM Cost
BOM cost is defined as the total cost associated with all the components listed in the Bill of Materials required to build a product, along with the costs related to the actual assembly and production process. It represents the sum of costs for raw materials, labor, and any additional costs attributable to the manufacturing of the product. The BOM cost facilitates a detailed understanding of product cost structures and helps businesses in financial planning, cost management, and setting the retail price that ensures a sustainable profit margin.
To elaborate, the BOM cost includes various cost components such as:
- Raw materials
- Labor costs
- Cost of materials like passive and active components
- Overhead costs, such as equipment or factory space
- Supplier costs, including shipping and handling
- Hidden costs like waste, scrap, or quality control
Importance of BOM Cost in Manufacturing
Understanding the BOM cost is pivotal for manufacturers as it directly impacts numerous aspects of the business, including profitability, competitive pricing, and inventory management. A well-documented BOM cost allows for a clear view of actual costs, aiding in the calculation of standard costs and active cost records. This knowledge is instrumental in formulating strategies for cost reduction while maintaining product quality.
Moreover, the BOM cost is essential in various stages of production planning and management software, ensuring that an organization can anticipate and respond to market conditions effectively. A thorough analysis of BOM costs helps businesses to keep track of average costs and assess supplier performance, laying the groundwork for negotiations and better sourcing decisions.
With the fluctuating prices of raw materials and the dynamic nature of labor costs, having precise and updated BOM costs can mean the difference between a profitable venture and a financial misstep. It also provides insights into potential economies of scale that can be leveraged when ordering component quantities in bulk.
In summary, BOM cost is a comprehensive accounting of all costs involved in the manufacturing process, from procurement of raw materials to the final assembly, encompassing direct costs, indirect costs, and the hidden costs that can sometimes be overlooked. Its significance in manufacturing cannot be overstated, as it ensures profitability, informed decision-making, and strategic planning for businesses.
Factors Affecting BOM Cost
The Bill of Materials (BOM) cost is influenced by several factors that can fluctuate over time, impacting the overall cost of manufacturing a product. These factors include the prices of raw materials, the costs associated with individual components, labor costs, the efficiency and type of manufacturing processes, overhead expenses, and inventory costs. Each element holds the potential to either increase or decrease the final BOM cost, making it critical for businesses to continuously monitor and optimize these expenses.
Raw Materials
The cost of raw materials encompasses the expenses for all basic materials required to construct a product. Market conditions significantly affect these costs, as they are subject to global supply and demand fluctuations, geopolitical events, and natural resource availability. A spike in raw material costs directly translates to an increased BOM cost. Manufacturers must adapt by either absorbing the costs, which reduce profit margin, or passing them onto consumers in the form of higher retail prices.
Component Costs
Components in the BOM can include everything from passive elements like resistors and capacitors to more complex active elements such as microchips and displays. The unit prices of these components are vital factors in calculating the BOM cost. Component costs are influenced by supplier pricing, Component quantities ordered (with bulk orders typically reducing per-unit cost), and technological advancements that may render certain parts more expensive or obsolete.
Labor Costs
Labor costs reflect the human capital required to assemble and produce the final product. They can vary widely based on geographic location, skill levels, and labor market conditions. An increase in labor costs due to wage inflation or a shortage of skilled workers leads to higher production costs, affecting the overall BOM. Efficient production planning can help mitigate these costs by optimizing labor force productivity.
Manufacturing Processes
The chosen manufacturing processes play a critical role in determining BOM cost. Some processes may offer cost efficiencies but require higher upfront investment in specialized machinery, while less expensive methods may be slower or less precise, resulting in increased waste and higher indirect costs. A balance must be struck to select a process that meets both quality standards and cost-effectiveness.
Overhead Costs
Overhead costs include all expenses not directly tied to production, such as utilities, rent for factory space, equipment depreciation, and factory maintenance. These are generally fixed costs, but they can fluctuate with changes in production volume or business scale. Effective cost management must consider reducing overhead where possible without compromising operational efficiency.
Inventory Costs
Inventory costs encompass the expenses associated with storing and managing raw materials and components before they are used in production. High inventory levels can lead to increased costs due to storage fees, potential obsolescence, and tied-up capital. On the other hand, too little inventory can lead to production delays and missed opportunities. Inventory management software and just-in-time inventory practices can help minimize these costs.
By carefully analyzing and managing each of these factors, businesses can achieve a clear and accurate understanding of their BOM cost, ensuring that their products remain profitable and competitively priced. Effective monitoring and cost control are crucial to maintaining a healthy balance between quality, production efficiency, and cost-effectiveness.
BOM Cost Optimization Strategies
To navigate the complex landscape of manufacturing costs, businesses should employ a suite of BOM cost optimization strategies. These strategies are designed to streamline expenses without sacrificing the quality of the finished product. Through a combination of smart purchasing decisions, efficient production practices, and judicious cost management, companies can improve their bottom line and remain competitive in ever-changing market conditions. Below, we delve into each strategy to provide actionable insight into reducing and managing BOM costs effectively.
Cost Reduction Opportunities in Raw Materials
Securing cost reduction opportunities in raw materials requires proactive market analysis and strategic sourcing. Establishing long-term relationships with suppliers can lead to negotiated discounts or bulk purchasing incentives. Exploring alternative materials that meet the product specifications but come at a lower cost can also yield significant savings. Furthermore, considering the use of recycled or reclaimed materials not only reduces cost but also enhances the sustainability profile of the product.
- Negotiated supplier contracts
- Alternative materials evaluation
- Bulk purchasing discounts
- Recycled materials utilization
Efficient Component Selection and Pricing
Choosing the right components at the right price is essential for BOM cost efficiency. This means selecting reliable yet cost-effective suppliers and regularly reviewing component specifications to find alternative parts with a better price-performance ratio. It’s also important to stay abreast of new technological advancements that could provide more economical options. Establishing partnerships with multiple suppliers can create a competitive environment, ensuring the best pricing without compromising on component quality.
- Supplier cost comparison
- Component specification review
- Alternative part evaluation
- Multiple supplier partnerships
Streamlining Labor Costs
Labor costs can be streamlined by investing in worker training and development, improving the skillset of the workforce, and increasing productivity. Implementing automated processes where possible can also reduce the dependence on manual labor, leading to long-term cost savings. Furthermore, adjusting production schedules to avoid overtime and creating efficient workflows can minimize labor hours and associated costs.
- Workforce training programs
- Automation of manual processes
- Production schedule optimization
- Workflow efficiency improvements
Improving Manufacturing Processes for Cost Efficiency
Enhanced manufacturing processes often result in lower costs by reducing waste and increasing throughput. Upgrading equipment to more modern, energy-efficient models can cut operational expenses substantially. Additionally, adopting lean manufacturing principles can help to identify and eliminate inefficiencies throughout the production cycle, from material sourcing to final assembly.
- Equipment modernization and efficiency
- Lean manufacturing implementation
- Waste reduction initiatives
- Throughput enhancement techniques
Effective Inventory Management
Effective inventory management strikes the balance between having enough stock to meet demand and minimizing storage costs. Utilizing just-in-time inventory systems reduces carrying costs and diminishes the risks of obsolescence or excess stock. Inventory management software can offer real-time insights, allowing for more accurate forecasting and planning, ultimately reducing unnecessary inventory holdings.
- Just-in-time inventory systems
- Real-time inventory management software
- Accurate forecasting methods
- Inventory holding cost minimization
Consideration of Overhead Costs
Overhead costs must be carefully reviewed and managed to ensure they do not erode the company’s profit margins. Simple measures such as energy-saving initiatives and regular maintenance can prevent costly downtime and extend the life of equipment. Reevaluating service contracts and renegotiating terms can also lead to overhead savings. It’s vital that a business continually seeks out new methodologies and technologies to lower these fixed costs where feasible.
- Energy-saving measures
- Preventive equipment maintenance
- Contract renegotiation strategies
- Continuous overhead cost review
By diligently applying these optimization strategies to the BOM cost, businesses can enhance their financial resilience. The effective management of materials, components, labor, manufacturing processes, inventory, and overhead brings about a structured approach to slashing costs without diminishing the essence of the product offered to the consumers.
Tools and Methods for BOM Cost Analysis
Effective cost analysis of a Bill of Materials (BOM) is crucial for manufacturers to remain profitable and competitive. By leveraging various tools and methods, businesses can gain insights into actual costs and identify potential savings. Cost estimation software, spreadsheet templates, and process mapping are commonly used to break down and scrutinize the different cost categories. These tools can provide detailed visibility into each component’s cost, including raw materials, labor, overhead, and other indirect expenses. The use of standardized methods ensures consistency and accuracy in cost analysis, which is vital for making informed decisions. As a further step, techniques like activity-based costing (ABC) can attribute costs more accurately to individual products or services by identifying cost drivers and linking them to specific activities.
Cost Estimations and Calculations
Cost estimations and calculations form the backbone of BOM analysis. Manufacturers need to determine the unit prices of individual components, labor charges per hour, overhead costs, and factor in any hidden costs that might emerge during the manufacturing process. Each of these cost components has to be calculated with precision, considering market conditions and supplier costs. Predictive analytics and regression analysis are methods that can be used to forecast future cost changes and prepare for market fluctuations. Calculations must be detailed, yet flexible enough to accommodate changes in pricing, currency exchange rates, and other variables that can impact the total cost.
Software for BOM Cost Management
To streamline the management of BOM costs, many companies turn to specialized software solutions. These platforms can automate the collection of cost data, perform real-time calculations, and provide dashboards for monitoring cost trends. Software solutions can integrate with inventory management systems to assist in production planning and offer features like “what-if” analysis to simulate the impact of cost changes. Some advanced BOM management software also includes collaboration tools, enabling teams to work together on cost optimization. Enterprise Resource Planning (ERP) and Material Requirements Planning (MRP) systems can offer additional layers of cost management, synchronizing financial data across the entire operation.
Should-Cost Analysis
Should-cost analysis is a proactive costing technique aimed at determining what a product should cost based on its design parameters, manufacturing processes, and raw material requirements. Rather than looking at historical data or supplier quotations, should-cost analysis sets a benchmark for negotiating prices with suppliers and identifying cost reduction opportunities. It involves a deep dive into the manufacturing process, evaluating cost drivers and identifying areas where efficiencies can be improved. This forward-looking method promotes strategic decision-making by projecting the expected costs of production.
Multi-Level BOMs and Bills of Materials
Multi-Level BOMs are complex structures that provide a granular view of the production process by breaking down a product into its sub-assemblies, components, and parts at various levels of detail. These hierarchical documents not only list materials needed but also outline the relationship between different parts and their assemblies. Managing multi-level BOMs is essential for accurate cost roll-ups and ensuring that all indirect costs, such as adhesives and fasteners, are accounted for. Accurate multi-level BOMs aid in reliable cost estimation and help in identifying bottle necks in the production process that may lead to cost increases.
Using Historical Data for Cost Analysis
Historical cost data is invaluable for BOM cost analysis as it provides context and benchmarks for current cost estimations. By examining past data, manufacturers can identify trends, recognize patterns of cost fluctuation, and make informed predictions about future costs. Historical data facilitates variance analysis, which can shed light on discrepancies between estimated and actual costs, highlighting areas for improvement. Companies should maintain active cost records, regularly updating them to ensure they reflect the latest market dynamics and internal efficiencies. This continuous process aids in refining standard costs, adjusting pricing strategies, and calculating the average cost for more accurate budgeting and forecasting.
Case Studies in BOM Cost Optimization
Manufacturers continuously seek ways to refine their Bill of Materials (BOM) to improve margins, reduce waste, and respond effectively to competitive markets. Through case studies of companies like Orange Electronics and Acme Electronics, valuable insights into the process and benefits of BOM cost optimization can be gained. These real-world scenarios illustrate how businesses approach cost challenges and implement solutions, providing a roadmap for others looking to streamline their own manufacturing processes.
Case Study 1: Orange Electronics
Orange Electronics, a mid-sized company specializing in consumer electronics, faced rising costs due to increased raw material prices and labor charges. By conducting a thorough analysis of their BOM, the company identified several areas where costs could be curtailed. They found success by:
- Negotiating better rates with suppliers, leveraging long-term contracts to secure more favorable prices on raw materials.
- Implementing cost estimation software to provide more accurate and transparent cost management.
- Streamlining labor processes through better production planning, which reduced overtime expenses.
- Identifying alternative materials that maintained product quality while reducing the cost of materials.
As a result, Orange Electronics saw a significant reduction in their overall product cost, enhancing their competitiveness in the market.
Case Study 2: Acme Electronics
Acme Electronics, known for their high-quality audio equipment, embarked on a cost reduction initiative to preserve their profit margins without compromising on the quality that their customers had come to expect. The strategic measures they took included:
- Adopting lean manufacturing processes to eliminate waste in every stage of their manufacturing process.
- Conducting should-cost analysis to establish a clearer understanding of what the components should cost, which enabled better negotiations with suppliers.
- Utilizing MRP software to tighten inventory management, reducing the costs tied to excess stock.
- Engaging in value engineering to examine the utility of each component, leading to simplified product designs that maintained sound quality with fewer or less expensive parts.
Acme Electronics’ efforts resulted in an impressive decline in BOM costs while maintaining the high standards of their finished products.
Lessons Learned and Best Practices from Successful Cost Optimization Projects
The experiences of Orange Electronics and Acme Electronics provide several lessons and best practices for effective BOM cost optimization:
- Regularly review and renegotiate supplier contracts to capture the most competitive material costs.
- Embrace technology, such as BOM cost management software, for enhanced accuracy and real-time monitoring.
- Apply lean principles to reduce waste and optimize labor productivity.
- Use should-cost analysis to understand and justify the cost structure of a product.
- Prioritize value engineering to ensure every component of a product contributes to its value proposition.
- Foster a culture of continuous improvement, encouraging staff to identify and act upon cost reduction opportunities.
In any cost optimization project, having a committed, cross-functional team focused on relentless cost management is critical. By applying these lessons and best practices, companies can effectively manage their BOM costs, improve profitability, and stay agile in an ever-changing market.
Note: The two case studies listed above are fictional examples created for illustrative purposes.
Challenges and Considerations in BOM Cost
When managing the Bill of Materials (BOM) cost, manufacturers face numerous challenges that affect their ability to accurately estimate and control expenses. Here are some key considerations and challenges:
- Raw Material Volatility: The cost of raw materials can be highly volatile, influenced by market conditions, geopolitical events, natural disasters, and commodity price swings. This unpredictability challenges manufacturers to keep BOM costs stable.
- Labor Cost Fluctuations: Wage rates can vary greatly depending on geographic location, labor market dynamics, regulatory changes, and industry competition, impacting the cost of assembling and producing goods.
- Complex Manufacturing Processes: Each step in manufacturing can add layers of cost, and optimizing these processes requires in-depth analysis and streamlining efforts which are resource-intensive.
- Inaccuracy in Cost Estimation: Estimating the costs of individual components and processes can lead to inaccuracies, especially if not using advanced cost management software or methodologies.
- Component Sourcing and Logistics: Procuring components from suppliers and managing the logistics of delivery can introduce additional costs, such as tariffs, transportation, and warehousing expenses.
- Changes in Technology: Technological advances may render certain components obsolete or necessitate upgrades, thereby influencing both the unit prices and the need for redesigning products.
- Supplier Negotiations: The ability to negotiate better terms with suppliers can significantly affect the BOM cost, but this often requires considerable time and expertise.
- Hidden Costs: Often overlooked, hidden costs such as machine setup time, quality control, and maintenance can accumulate and impact the overall BOM cost.
- Cost Reduction Pressures: Continuous pressure to lower costs without sacrificing quality can lead to challenging trade-offs and the risk of cutting critical corners.
- Inventory Management: Efficient inventory management is crucial; overstocking leads to higher carrying costs, while understocking can result in production delays and expedited shipping charges.
Price Fluctuations in Component Prices
Component costs are subject to frequent changes, which can be a significant hurdle when managing a BOM. Several factors contribute to the fluctuations in component prices:
- Supply and Demand: The most fundamental economic principle affects component prices. Shortages of components can lead to bidding wars and price increases, while oversupply may result in price drops.
- Currency Exchange Rates: With global supply chains, variances in currency exchange rates can notably affect the cost when importing components from different countries.
- Commodity Prices: For components relying on commodities like copper, steel, or plastics, changes in commodity pricing on international markets directly impact component costs.
To illustrate how these fluctuations impact BOM costs, consider the following table of hypothetical component price changes:

The above table is a simplification, but it serves to underline the dynamic nature of component pricing and the need for vigilant BOM cost management. Strategies to mitigate these fluctuations could include diversifying suppliers, entering into long-term purchasing agreements, or investing in commodity hedging to lock in prices.
Navigating these challenges is about balancing cost objectives with production needs and market demands. This requires a strategic approach to supply chain management, a keen understanding of market trends, and the ability to act swiftly to adjustments in the BOM. Manufacturers that master these complexities can sustain profitability even in the face of unpredictable component pricing.