Selecting the right brushless motor controller is critical for optimizing performance in various applications, from robotics to electric vehicles. Brushless DC (BLDC) motors, favored for their efficiency and reliability, demand controllers that align with their specific working principles and types. Understanding the nuances of different controller types—such as SBL, KBL/MBL, FBL, and GBL—is essential for ensuring effective operation tailored to individual needs.
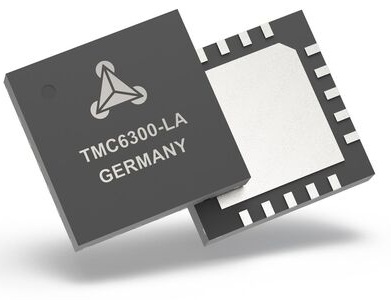
Controllers must feature robust architecture, be compatible with sensors, and deliver efficient sine wave control to maximize motor performance. With diverse applications ranging from industrial tools to automotive systems, the role of these controllers becomes even more significant, making the right choice vital for achieving high-speed performance, energy efficiency, and proper thermal management.
This article delves into the complexities of brushless motor controllers, discussing key features, application areas, and technical considerations essential for choosing the ideal controller for your needs. Explore how these components can propel innovation and efficiency in your projects as we guide you through the selection process.
Understanding Brushless DC (BLDC) Motors
Brushless DC (BLDC) motors are a type of electric motor that offer efficient and quiet operation. Instead of brushes, they use electronic controllers to switch current, making them more reliable than traditional motors. The permanent magnets within the motor rotor interact with the stator’s electromagnetic field, which is controlled by a BLDC motor controller. This method of operation provides better performance and longer motor life. BLDC motors are popular in many fields due to their energy efficiency and minimal maintenance needs. They find applications in industrial settings, electric vehicles, and even in personal gadgets like drones and electric scooters.
Working principles of BLDC motors
The working principles of BLDC motors revolve around their unique structure and electronic commutation. These motors do not have brushes; instead, they rely on a BLDC motor controller to manage the flow of current through the stator windings. This creates a rotating magnetic field that causes the rotor, embedded with permanent magnets, to turn. The controller uses sensors to detect the position of the rotor, ensuring that the magnetic fields are in sync for smooth operation. As a result, BLDC motors offer precise speed control and efficient energy use, minimizing energy costs and enhancing performance.
Types of BLDC motors
There are several types of BLDC motors, each suited to different applications. The most common distinction is between inner rotor and outer rotor designs. Inner rotor motors have the rotor inside the stator, which allows for high-speed and stable performance. This design is typically used in power tools and industrial applications. On the other hand, outer rotor motors have the rotor on the outside of the stator, providing more torque and slower speed. They’re often employed in applications where quiet operation and stability are essential, such as in fans or electric scooters. Each type offers unique benefits, enabling a wide range of uses and design flexibility.
Types of Brushless Motor Controllers
A brushless motor controller is an essential component in many electronic devices. These controllers manage the function of brushless DC motors (BLDC). They offer benefits like energy efficiency, quiet operation, and smooth performance. There are various types of brushless motor controllers, such as SBL, KBL/MBL, FBL, and GBL. Each serves different needs in a wide range of industrial applications. By converting electrical energy into mechanical motion, these controllers optimize power use and improve device performance. Understanding the different types can help you select the right controller for specific applications.
SBL Controllers
SBL controllers are known for their advanced features and reliability. They are ideal for applications where precise motor control is necessary. These controllers can handle various current ratings, making them versatile. SBL motor controllers often include programmable options for customization. This allows users to fine-tune the motor’s performance. Features like Field Oriented Control (FOC) enable efficient control over the magnetic field in the motor. This results in smooth and efficient motion, which reduces energy costs and extends the motor’s life.
KBL/MBL Controllers
KBL and MBL controllers specialize in providing robust performance for heavier loads. They are perfect for industrial applications where durability is key. These controllers can handle larger permanent magnets and deliver reliable power output. KBL/MBL controllers are often used in electric motors for industrial machines. They balance speed and torque, making them ideal for demanding tasks. With their wide range of current ratings, these controllers can adapt to various power needs. Their design flexibility supports time to market readiness for new products.
FBL Controllers
FBL controllers focus on offering quiet operation and precise control. These controllers are suitable for applications where minimal noise is a priority. They use a technique that controls speed with great accuracy, ensuring energy-efficient performance. FBL controllers are often seen in electric scooters and consumer appliances. Their ability to reduce noise makes them a preferred choice in environments where quiet operation is critical. With advanced technology, these controllers keep power supply demand low while maintaining excellent performance.
GBL Controllers
GBL controllers are known for their high-power capabilities and robustness. They are used in applications requiring significant power, such as large electric motors. Their design supports heavy-duty operations while ensuring efficiency. GBL controllers use innovative technology to handle varying loads and maintain stability. They are widely used in areas like transportation and large equipment. These controllers support advanced features and are easily programmable, allowing for tailored performance adjustments. With strong power wires and components, they offer reliable operation even under high stress.
Key Features and Capabilities of Controllers
Brushless motor controllers are crucial components that manage the performance of brushless motors, widely used for their efficiency and smooth operation. These controllers provide precise control over speed, torque, and position, making them ideal for various applications. With advanced features such as programmable settings and field-oriented control, these controllers enhance motor responsiveness and energy efficiency. They support a wide range of power ratings and are compatible with different types of motors, including those that use permanent magnets. Their design flexibility allows for adaptation to specific industrial applications, reducing time to market. Moreover, brushless motor controllers contribute to energy savings by optimizing power consumption.
Architecture and design of controllers
The architecture and design of brushless motor controllers play a significant role in their performance. They typically incorporate elements like power supply circuits, control algorithms, and communication interfaces. The main goal is to convert electrical energy efficiently while maintaining smooth and quiet motor operation. Key design features include efficient heat dissipation to handle high power outputs without overheating. Modern controllers are compact and lightweight, facilitating easy integration into various devices such as electric scooters and industrial machinery. The thoughtful design also includes robust protection mechanisms to guard against short circuits and overloads, ensuring the longevity and reliability of both the controller and the motor.
Sensor compatibility and requirements
Brushless motor controllers often require sensors to provide feedback for accurate control. These sensors detect magnetic fields and motor position, enabling precise management of speed and torque. Common sensor types include Hall effect sensors and encoders. Hall sensors measure the position of the motor shaft, while encoders offer high-resolution data on speed and angle. The compatibility of these sensors with controllers is crucial for effective operation. Controllers must be designed to read and interpret sensor signals accurately and quickly. This sensor-controller synergy ensures smoother operation and enhances the overall efficiency and reliability of the motor system.
Sine wave control efficiency
Sine wave control is a key method used in brushless motor controllers for achieving efficient operation. This technique involves driving the motor with a sinusoidal current, which closely matches the natural motion of the motor. This results in reduced vibrations and less noise, contributing to the quiet operation of the motor. Sine wave control also increases energy efficiency by optimizing power delivery and reducing energy costs. It enhances the performance of the brushless motor by providing a smoother torque output, minimizing wear and tear on the motor components. The efficiency gained from this control method makes brushless motor controllers ideal for applications requiring precision and silence.
Application Areas for Brushless Motor Controllers
Brushless motor controllers have revolutionized the way we use electric motors today. They provide efficient control over speed and torque, making them suitable for a wide range of applications. These controllers are essential for operating Brushless DC (BLDC) motors, which are known for their quiet operation and energy efficiency. This makes them ideal for many industries, from robotics to electric vehicles. Let’s explore some specific application areas where brushless motor controllers are making a significant impact.
Use in Robotics
In the realm of robotics, brushless motor controllers play a crucial role. Robots often require precise movements and varied speed control. Brushless motor controllers enable these robots to perform tasks smoothly and efficiently. With advanced features like programmable settings and Field Oriented Control, these controllers provide the flexibility needed for complex robotic maneuvers. The quiet and smooth operation of brushless motors is another reason they are favored in robotics. This quiet operation is crucial in environments that demand low noise. Additionally, these controllers help reduce energy costs which is important for long-term robotic deployments.
Industrial Tool Applications
Industrial tools benefit greatly from the use of brushless motor controllers. These tools often need high power and consistent performance over extended periods. Brushless motor controllers offer the reliability and power efficiency that industrial settings demand. They ensure that tools such as drills, saws, and grinders operate at optimal conditions. Current ratings and programmable features of these controllers allow for better energy management and speed control. This is essential in environments where precision and reliability are paramount. Industrial applications also favor these controllers due to their design flexibility, which allows them to fit various tool designs and specifications.
Automotive and Electric Vehicle Integration
In the automotive industry, especially in electric vehicles, brushless motor controllers are indispensable. They manage the electric motors that propel these vehicles, optimizing speed and torque for different driving conditions. The integration of these controllers in electric scooters and 500W electric bikes highlights their adaptability. Brushless motor controllers enhance the performance of electric vehicles while improving their energy efficiency. They support permanent magnet motors and can handle varying current ratings. This is critical in providing smooth acceleration and deceleration, leading to better driving experiences. As the demand for electric vehicles rises, the need for effective motor controllers grows, shortening the time to market and pushing advancements in this field.
Technical Considerations for Selection
When selecting a brushless motor controller, it’s important to consider several technical factors. These controllers are key to ensuring smooth and efficient operation of brushless motors (BLDC motors). Their role includes adjusting the speed, direction, and torque of the motor. Understanding these factors helps in maintaining energy efficiency and maximizing the lifespan of the motor. It is also essential to consider the application area, as different uses might require specific features or capabilities like quiet operation and energy savings. This is particularly true for industrial and commercial applications, where the demands on motors can be substantial.
Motor Speed Control Challenges
Controlling the speed of a brushless motor involves specific challenges. Motors used in various applications need to operate at different speeds depending on their tasks. Achieving precise speed control can be complicated due to the different loads that motors might face. Variations in load can affect the speed, requiring the controller to adjust quickly to maintain performance. Advanced features in controllers, such as programmable settings, can address these challenges. Incorporating such features helps in adapting to varying loads and achieving steady speed regardless of conditions. Proper motor speed controllers are crucial for avoiding wear and ensuring reliability, particularly in demanding industrial settings.
Role of DC-to-DC Converters
DC-to-DC converters play a vital role in the operation of brushless motor controllers. They are responsible for converting voltage levels to match the motor’s requirements. By doing so, they ensure that the motor receives the appropriate power supply. This conversion is critical for maintaining efficiency and reducing energy costs. These converters also offer design flexibility, allowing motor controllers to be used in a wide range of applications. Their presence in a system ensures consistent power delivery, helping in the smooth operation of motors. In electric scooters and other vehicles, they help in extending battery life by optimizing energy consumption.
Controller Circuit Design Parameters
The design parameters of a controller circuit greatly impact the performance of a brushless motor controller. These parameters include current ratings, power wires, and the ability to handle different time to market needs. Properly designed circuits ensure efficient energy usage and reduce the risk of overheating or damage. Understanding the magnetic field and its interaction with permanent magnets within the motor is also vital. These elements ensure the smooth and quiet operation of the motor. Field Oriented Control is one advanced technique used to manage these interactions for enhanced performance. A well-designed circuit addresses all these factors, ensuring the motor’s longevity and efficiency.
Ensuring Optimal Performance
A brushless motor controller is key to enhancing the performance of your electric motor systems. These controllers manage and regulate the speed and efficiency of brushless motors. With the right controller, you can achieve smooth operation and quiet performance. They use advanced features like Field Oriented Control to improve accuracy and responsiveness. Whether you’re working with electric scooters or industrial applications, these programmable brushless controllers offer design flexibility and precision. By understanding how to pair these controllers with the right applications, you not only optimize motor function but also extend equipment lifespan.
Importance of High-Speed Technology
High-speed technology is essential in modern brushless motor controllers. It enables precise control over motor speed, crucial for applications requiring fast response times. Using a high-speed brushless motor controller ensures smooth transitions and quick adjustments. This is particularly important in industries where time to market is critical, and advanced features are needed to stay competitive. By reducing lag and improving speed, controllers enhance the overall performance of Brushless DC motors. They also support a wide range of current ratings, allowing for various uses from small electronic devices to large industrial equipment.
Energy Efficiency Considerations
Energy efficiency in brushless motor controllers helps reduce energy costs and environmental impact. These controllers are designed to optimize the electrical flow within the motor, using permanent magnets to minimize energy loss. This results in less power consumption while maintaining high performance. An efficient brushless controller contributes to lower operational costs and increased equipment lifespan. Reducing energy waste not only benefits the user financially but also supports sustainable practices. For devices like those in electric scooters and industrial applications, efficient energy use is crucial for both economic and ecological reasons.
Cooling Capabilities and Thermal Management
Effective cooling capabilities are vital for the thermal management of brushless motor controllers. Proper thermal management prevents overheating, ensuring that motors run smoothly. Overheated components can lead to motor malfunction or failure, so keeping temperatures regulated is crucial. This is often achieved through inventive design and materials that dissipate heat quickly. Some controllers come with built-in features that monitor temperature in real-time. By minimizing heat-related wear and tear, these controllers extend the motor’s lifespan. Additionally, efficient cooling supports quiet operation, which is advantageous in both consumer and industrial settings.
Choosing a Brushless Motor Controller
When choosing a brushless motor controller, several factors should guide your decision.
- Motor Compatibility: Ensure the controller matches your motor’s type, such as a BLDC motor, and is compatible with its specifications.
- Power Supply: Verify that the controller can handle the voltage and current requirements of your motor.
- Speed Control: Look for a brushless motor speed controller that offers adjustable speed settings and supports smooth operation.
- Current Ratings: Make sure the controller’s current ratings meet or exceed those of your motor to avoid overheating.
- Advanced Features: Consider controllers with Field Oriented Control for improved efficiency and programmable options for design flexibility.
- Industrial Applications: If needed, select a controller suitable for specific industrial applications, ensuring a wide range of functionalities.
- Quiet & Energy Efficient: Choose controllers known for quiet operation and energy efficiency, reducing overall energy costs.
By considering these points, you can select a brushless motor controller that suits your needs perfectly.