In the intricate world of semiconductor manufacturing, the integrity of every component is paramount. Enter the burn-in socket, a seemingly simple but crucial tool designed to stress test semiconductors, ensuring they can operate reliably under various conditions. As tech advances, the demand for semiconductors that can withstand rigorous stress without failure has never been greater, and burn-in sockets play a vital role in this quality assurance process.
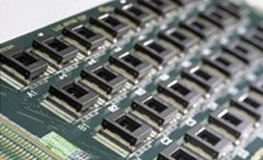
A burn-in socket is not just your average integrated circuit (IC) holder; it is a specialized device engineered for rigorous testing environments. These sockets differ from standard IC sockets by providing features that accommodate extended testing and high-temperature operations, crucial in identifying potential device failures before they reach the consumer. By facilitating extended testing periods, burn-in sockets significantly boost the reliability of semiconductor devices, ensuring they meet the stringent demands of modern applications.
In this article, we’ll explore the essence of burn-in sockets, dive into their importance in semiconductor manufacturing, and examine the various types available. We’ll also offer guidance on selecting the most effective burn-in socket for your needs, considering factors like compatibility and cost-effectiveness. Stay tuned as we uncover innovations and trends shaping the future of burn-in socket technology, and highlight the advantages of collaborating with industry-leading manufacturers.
What is a Burn-In Socket?
A burn-in socket is a specialized tool used in the testing of electronic devices, particularly semiconductors. It is designed to hold and test components under stress, ensuring they function correctly even in harsh conditions. By using a burn-in socket, manufacturers can identify initial defects and improve the yield rate of semiconductors. These sockets are crucial in various industries, including automotive applications, where reliability and performance in high-temperature environments are essential. As the demand for durable and efficient electronic devices grows, the use of burn-in sockets becomes increasingly important.
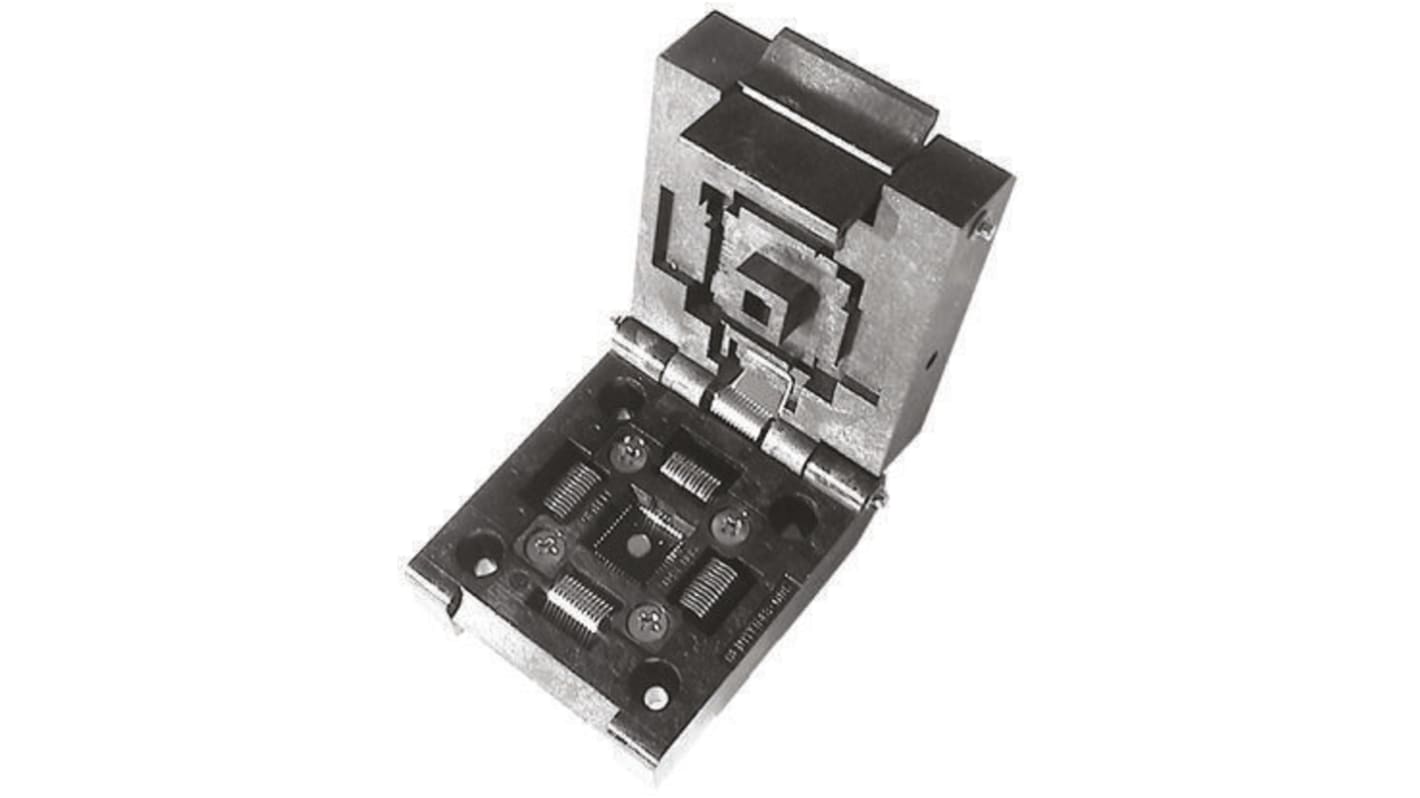
Definition and Purpose
A burn-in socket is a type of IC socket that is mainly used for burn-in and system-level testing of electronic devices. Its primary purpose is to subject semiconductors to prolonged periods of operational stress. This helps in identifying and eliminating defective products before they hit the market. By enduring high temperatures and demanding conditions, burn-in sockets play a pivotal role in testing a wide variety of products. This ensures that only robust and reliable components make it to the end-user, thereby enhancing the overall quality and performance of electronic devices.
Key Functions in Semiconductor Testing
Burn-in sockets are integral to semiconductor testing for several reasons. They allow for electrical testing and thermal performance assessment, ensuring that semiconductors meet industry standards. These sockets also facilitate the testing of semiconductors under operational conditions simulating real-world usage. By doing so, they help identify defective products early in the development of semiconductors. This process not only improves the reliability of products but also boosts the yield rate of semiconductor manufacturing. Moreover, burn-in sockets are adaptable, accommodating various package-specific designs and meeting the specific needs of automotive and other high-stakes applications.
Differences from Standard IC Sockets
Burn-in sockets differ significantly from standard IC sockets in terms of design and function. While standard sockets are used for general electrical connectivity, burn-in sockets are built for endurance testing. They often feature materials and socket bodies designed to withstand high temperatures and harsh conditions. The contact pins in burn-in sockets are engineered for repeated use without degradation, which is vital for long-duration tests. Additionally, burn-in sockets support a wide variety of semiconductors, including manual sockets, semi-custom sockets, and custom sockets. These features make them indispensable for rigorous testing processes where precision and durability are crucial.
Importance of Burn-In Sockets in Semiconductor Manufacturing
Burn-in sockets play a crucial role in the production of semiconductors. They are used to test electronic devices under harsh conditions. This process checks for initial defects in products. Burn-in testing ensures that only reliable products move forward in the production line. By doing so, manufacturers can meet the high demand for dependable electronic components. This testing is especially vital in industries like automotive, where performance under stress is critical. Different types of semiconductors require various kinds of burn-in sockets, ensuring that each component undergoes rigorous evaluation.
Role in Identifying Potential Failures
Burn-in sockets are key tools in finding defects early in the semiconductor manufacturing process. During a burn-in test, electronic devices face high-temperature environments. This stress reveals any potential issues that might not show up during regular operation. By pinpointing these flaws, manufacturers can prevent defective products from reaching the market. This process helps improve the yield rate of semiconductor production. Early identification prevents costly recalls and maintains brand reputation. This stage of testing increases the confidence in product quality for both manufacturers and consumers.
Enhancing Reliability of Semiconductor Devices
Burn-in sockets contribute significantly to the reliability of semiconductor devices. By testing components under extreme conditions, they ensure that only robust products are released. These tests mimic real-life scenarios where the devices will be used. Custom sockets, including package-specific and semi-custom sockets, are designed for different product needs. This customization leads to effective testing for a wide variety of products. Moreover, burn-in boards equipped with these sockets make it easy to test multiple devices simultaneously, speeding up the process. Testing also includes checking the thermal performance of semiconductors, further guaranteeing reliability.
Applications That Use Burn-In Testing
A variety of industries rely on burn-in testing to ensure their products can withstand demanding conditions. Automotive applications, for instance, require components that function reliably over time and under stress. Burn-in sockets ensure these parts are defect-free before they are installed in vehicles. In the development of semiconductors, burn-in testing is also crucial in enhancing the quality of IC sockets and other electronic devices. Sockets need to have superior socket body designs and contact pins for effective testing. Additionally, these sockets play a role in electrical testing, where ensuring proper connectivity is vital to the product’s success.
Characteristics of an Effective Burn-In Socket
Burn-in sockets are crucial components in the testing of electronic devices. They play a significant role in identifying initial defects before devices reach consumers. Effective burn-in sockets ensure that a wide variety of products perform well under harsh conditions. Their design helps enhance yield rates and reduce defective products. The demand for burn-in sockets spans across various industries, including automotive applications. Their importance is reflected in their ability to operate in high-temperature environments and under pressures that mimic real-world scenarios. This makes them essential for testing semiconductors and ensuring the thermal performance of devices.
Durability and Longevity
Durability and longevity are key qualities of an effective burn-in socket. These sockets must withstand repeated testing cycles without degrading. This is especially vital in high-temperature environments where constant heating can cause material fatigue. A socket’s durability is often judged by its socket body’s material and its ability to maintain performance over time. Quality materials ensure that contact pins remain effective, supporting continuous electronic testing without loss of precision. Longevity is also linked to reducing the cost and frequency of socket replacements, making durable sockets a cost-effective choice for testing facilities.
High Workability and Precision
High workability and precision are vital for ensuring accurate testing results. Burn-in sockets must accommodate a wide variety of products, adapting to different types of semiconductors and package designs. This flexibility is often achieved through semi-custom sockets and single burn-in socket options. Precision in socket design ensures that contact pins align perfectly with the test devices, minimizing errors. This aspect is crucial in maintaining the integrity of test data. Manual sockets help achieve this level of precision, allowing technicians to make necessary adjustments for specific testing requirements.
Performance in Varied Conditions
Burn-in sockets need to maintain performance across varied conditions. This means functioning correctly in both controlled test environments and more severe conditions that simulate real-world scenarios. Factors such as humidity, temperature fluctuations, and vibration must not affect the socket’s reliability. The sockets are designed for thermal performance, ensuring electronic devices can withstand conditions they might face during actual use. These sockets also contribute to higher yield rates by identifying and addressing defects before devices are deployed. Such performance in varied conditions is essential, particularly for automotive products that encounter diverse environments.
Types of Burn-In Sockets
Burn-in sockets are essential tools used in the testing of electronic devices. They ensure that components can withstand harsh conditions, such as high temperatures. These sockets help identify initial defects in semiconductors, which improves product yield rates and reduces defective products. Burn-in testing is crucial for a wide variety of products, including automotive applications, where reliability is paramount. Burn-in sockets are categorized into various types based on their design and usage. Each type serves different needs, catering to various semiconductor packages and testing environments. Let’s explore the distinct kinds of burn-in sockets available.
Open Top Sockets
Open top sockets are popular in the testing of semiconductors due to their accessible design. These sockets feature a socket body with contact pins that allow easy insertion and removal of electronic devices. They are primarily used in environments where frequent testing and semiconductor development occur. Open top sockets are ideal for types of semiconductors that require minimal handling during testing. Their design promotes efficient thermal performance, making them suitable for use in high-temperature environments. Additionally, their simplicity supports package-specific sockets and manual testing processes, which can meet the demand for burn-in tests affordably.
Clamshell Sockets
Clamshell sockets are known for their robust design, providing secure connections for various electronics during testing. These sockets encapsulate the semiconductor within a clamshell-like enclosure, shielding it from outside factors. The enclosed design ensures optimal contact pin alignment, preventing the risk of initial defects that might lead to defective products. This design is particularly beneficial for automotive products, where testing must simulate harsh conditions. Clamshell sockets often feature semi-custom socket designs to accommodate unique package requirements. Such customization ensures that the socket performs well in a wide variety of testing applications.
Cardedge Sockets
Cardedge sockets are designed to facilitate easy engagement with burn-in boards during the testing process. These sockets feature a distinctive structure where the edges of the electronic device slide into the socket body. Cardedge sockets offer stability and secure connections, making them ideal for repeated use in testing protocols. They are well-suited for harsh conditions, as they hold firm even during rigorous thermal testing scenarios. The simple yet effective design of cardedge sockets ensures reliable testing increase for a variety of semiconductor types. This type of socket design is crucial in both high-temperature environments and demanding automotive applications.
Factors to Consider When Choosing a Burn-In Socket
When selecting a burn-in socket, several factors come into play to ensure the process is effective and efficient. A burn-in socket is crucial for testing electronic devices, especially when evaluating their performance in harsh conditions. This process is essential for spotting initial defects and improving the yield rate. The socket’s design should align with specific semiconductor types and requirements. Additionally, it must support high-temperature environments and a variety of products, such as those used in automotive applications. To get the best results, it’s important to consider compatibility, adaptability, and cost-effectiveness. By focusing on these factors, you can avoid defective products and enhance the overall testing quality.
Compatibility with Semiconductor Devices
Compatibility is a critical aspect when choosing a burn-in socket. It must match the electrical, thermal, and mechanical needs of the semiconductor devices. Different semiconductors demand different socket designs, with contact pins suited to the device’s needs. The socket body should align with the IC socket and package-specific sockets to ensure smooth testing. It is crucial to confirm that the socket fits the specific device to avoid testing issues. The right socket can lead to better thermal performance and prevent overheating, improving the semiconductor’s durability. Always consider the variety of semiconductors you are testing to ensure compatibility.
Adaptability to Testing Requirements
Adaptability is another factor when selecting a burn-in socket. Testing conditions can vary widely, so the socket should handle both manual and automated processes. Developing semiconductors often means testing a wide variety of parameters, from electrical performance to temperature endurance. Sockets must adapt to different burn-in tests and testing increases in demand. Semi-custom and custom sockets offer flexibility to meet diverse test situations. The socket should easily mount on burn-in boards to accommodate automotive products and high-temperature environments. By choosing adaptable sockets, testing becomes more efficient and caters to various semiconductors.
Cost-Effectiveness and Total Cost of Ownership
Cost-effectiveness is a practical consideration when selecting burn-in sockets. Though initial costs may vary, the total cost of ownership should reflect long-term benefits. A cost-effective socket reduces defective products, thus saving money in the long run. The demand for burn testing can increase, but investing in quality sockets prevents frequent replacements and failures. Consider both the upfront purchase cost and maintenance expenses. A reliable socket offers a high yield rate, ensuring fewer issues with electronic devices. Selecting the right socket balances cost with performance, providing value while maintaining testing quality.
Innovations and Trends in Burn-In Sockets
The field of burn-in sockets, crucial in testing electronic devices, continues to evolve. These sockets are essential for identifying initial defects before products reach consumers. Recent advancements focus on improving the socket body and ensuring compatibility with a wide variety of products. This enhances the ability to conduct burn-in tests efficiently. The demand for improved burn-in sockets is driven by the rising complexity of electronics. As electronic devices grow more sophisticated, the need for reliable testing methods increases. This results in innovations that boost thermal performance and adaptability to harsh conditions.
Customization and Design Flexibility
Customization in burn-in sockets is expanding to meet diverse needs. Semi-custom and package-specific sockets are now more available. This flexibility allows for solutions tailored to specific types of semiconductors. Design advancements ensure that sockets can withstand high-temperature environments and maintain integrity. Manufacturers are developing sockets with improved contact pins for better electronic connections. Custom solutions also enhance the yield rate by reducing defective products, especially in automotive applications. Manual sockets and single burn-in sockets are designed to cater to varied testing scenarios. Such flexibility ensures that electronic devices meet stringent quality standards.
Integration with Advanced Testing Technology
Integrating cutting-edge technology with burn-in sockets is revolutionizing electrical testing. Automation in testing processes is one such advancement that appeals to manufacturers. By using advanced socket designs, companies can better handle the testing of semiconductors. This results in a significant testing increase, offering better efficiency and accuracy. Such technology enables testing in high-temperature environments, preparing products for real-world conditions. It also supports faster assessment, reducing the time needed to identify faults. As technology advances, sockets will continue to serve as crucial components in the development of semiconductors.
Influences of Emerging Semiconductor Trends
Emerging trends in semiconductors impact burn-in socket design greatly. As semiconductors evolve, the corresponding sockets must adapt to new requirements. This includes addressing power increases and shrinking component sizes. The industry moves towards more compact and efficient solutions, which requires innovation in socket design. The rise of automotive products with complex electronic systems demands robust testing solutions. Sockets need to be versatile enough to work with a variety of products and withstand rigorous testing. The ongoing development of semi-custom solutions reflects the market’s push for more precise and dependable testing outcomes. These trends point to a future where burn-in sockets will remain central to electronic testing and quality assurance.
Advantages of Collaborating with Leading Manufacturers
Collaborating with leading manufacturers in the electronics industry offers numerous benefits. These manufacturers specialize in producing high-quality products such as burn-in sockets, essential for electronic testing and improving product yield rates. By partnering with these industry leaders, businesses gain access to not only premium products but also advanced technologies, which enhance their capabilities in testing semiconductors and other electronic devices. Furthermore, these manufacturers have established reputations, ensuring that the products developed are tested under harsh conditions, meeting global standards. This collaboration is key to maintaining competitive advantage and innovation in technology-driven markets.
Benefits of Partnerships with Innovative Companies
Partnering with innovative companies is crucial for those seeking to remain competitive in dynamic markets. Such partnerships allow businesses to access cutting-edge technologies and insights into new product developments. Innovative companies often lead the way in designing specialized sockets, like package-specific or manual sockets, enhancing the testing and development of semiconductors. These partnerships fuel progress by integrating diverse expertise, whether focusing on thermal performance or increasing electrical testing capabilities. As a result, businesses can introduce a wide variety of products that meet the growing demand for high-temperature environments and sophisticated automotive applications.
Global Support and Service Offerings
Working with leading manufacturers not only grants access to high-quality products like semi-custom and single burn-in sockets, but also extends comprehensive global support. These manufacturers often provide complete service offerings, ensuring that clients receive the necessary assistance in implementing and maintaining advanced testing systems. They offer expertise across various sectors including automotive and electronics, which helps businesses adapt to market changes and demands efficiently. Their global presence ensures that support is available around the clock, facilitating the seamless integration and operation of sophisticated technological solutions. This level of support is crucial for sustaining product reliability and performance across international markets.
Case Studies: Enplas, Yamaichi Electronics, Smiths Interconnect, Boyd Semiconductor
Examining case studies from leading companies like Enplas, Yamaichi Electronics, Smiths Interconnect, and Boyd Semiconductor reveals the tangible benefits of collaboration. Enplas, known for its custom socket solutions, improves yield rates by providing burn-in board testing suited to a variety of semiconductors. Yamaichi Electronics excels in creating IC sockets that handle initial defects with precision, enhancing product longevity. Smiths Interconnect focuses on robust contact pin technology, essential for succeeding in high-demand automotive applications. Boyd Semiconductor is synonymous with reliability, offering support for electronic devices under harsh conditions. These companies illustrate how partnerships lead to innovation and improved product performance.
Burn in Socket Pricing
Burn-in socket pricing can differ based on several factors such as design, type, and application. These sockets are essential for burn-in testing, which ensures that electronic devices work correctly under harsh conditions.
Types of Burn-In Sockets:
- Custom Sockets: Typically higher in price due to tailored design.
- Semi-Custom Sockets: Moderately priced; they balance customization and cost.
- Manual Sockets: Usually more affordable, ideal for easy handling.
- Single Burn-In Sockets: Economical choice for testing fewer units.
Price Influencers:
- Socket Design: Complex designs often cost more.
- Temperature Range: High-temperature environments require specialized, costlier materials.
- Semiconductor Type: Specific semiconductors need package-specific sockets, influencing price.
Price of Burn-In Sockets:
- Manual Sockets: $50 – $150
- Single Sockets: $100 – $250
- Semi-Custom Sockets: $200 – $500
- Custom Sockets: $500+