In our day to day lives, we use tens, if not hundreds of electronic devices, knowingly and unknowingly. Technology has gotten to a point where it is ubiquitous, with almost all the appliances, machines and devices in your home being powered by the semiconductor revolution.
From desktop computers, laptops, tablets, smartphones, and other items that we know are full of electronics, to cars, dish-washers, coffee machines, printers, and even fridges, they all have one thing in common: their functionality has come to rely more and more on small circuits, their ‘brains’ if you will. These circuits allow your car to regulate fuel and air intake, your computer to keep cool under heavy loads, and your coffee-maker to make you the best whipped-cream, double-frothy Frappuccino.
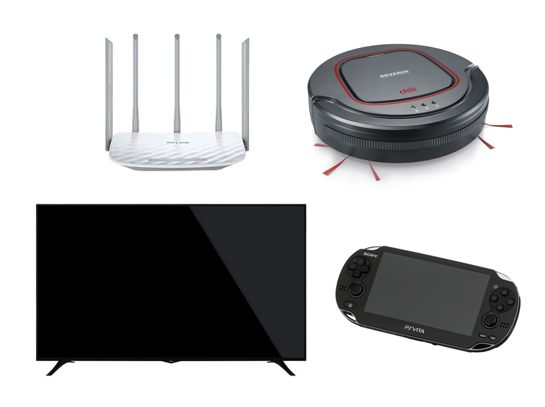
Brief History of Electronics Manufacturing
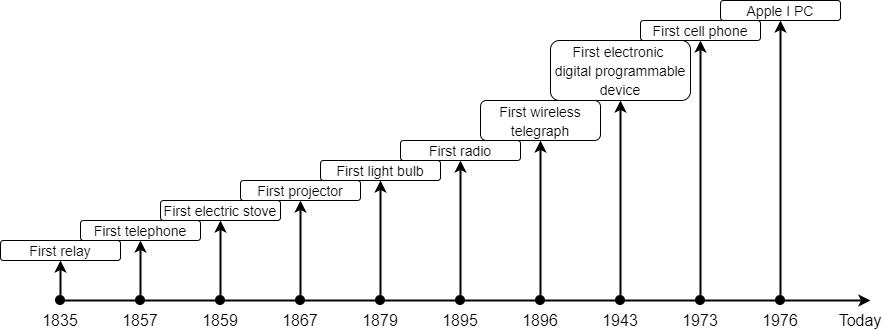
Figure 1 – History Timeline of Electronics’ Manufacturing
First of all, we need to look at where electronics manufacturing started from, for us to truly understand how far we have come and how far we (maybe) still have to go.
The very first electronic devices were hand-made, as they were very application specific. As such, the first one was invented by Joseph Henry in 1835 and it was a relay (although it’s disputed between him and Edward Davy). Then came the first telephone in 1857, by Alexander Graham Bell and Thomas Watson, the first electric stove in 1859, by George Simpson, the first projector in 1867, by William Lincoln, and, most famous of all, the first light bulb in 1879, by Thomas Edison.
The speed of new electronic devices kept increasing with time, getting the first radio in 1895, by Guglielmo Marconi, the wireless telegraph in 1896, also by Guglielmo Marconi, and, closer to the present day, the first electronic digital programmable device (Colossus Mark I) in 1943, the first cell phone in 1973, by Martin Cooper and the Apple I Personal Computer in 1976.
Electronic Manufacturing Processes and Workflows
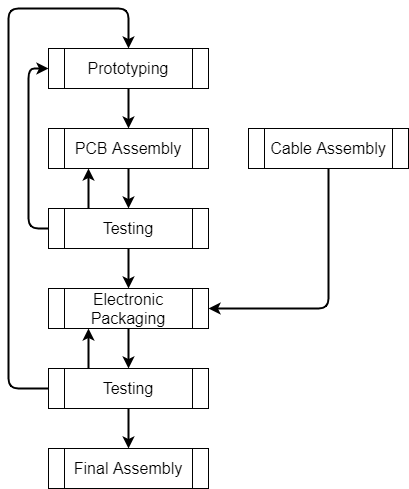
Figure 2 – Electronic Manufacturing Process
In the 19th and 20th century, with the ever increasing pace of electronic inventions, electronic manufacturing went from single prototypes, to basic assembly lines where people worked on a set of devices, and, closer to the 21st century, to the fully automated assembly lines, where robots produce at huge scales and in incredible quantities all the electronics that make life in the modern day possible.
Over time, complexity grew, both at the product level and at the assembly level, which resulted in more advanced electronic manufacturing techniques being developed and used to achieve higher quotas of production and higher levels of quality control.
The main processes behind electronics manufacturing today are as follows: fabrication and assembly of PCBs (short from Printed Circuit Boards), cable assembly, packaging, prototyping and testing. We will go into more depth into each of these and explore the technologies behind them.
PCB Assembly
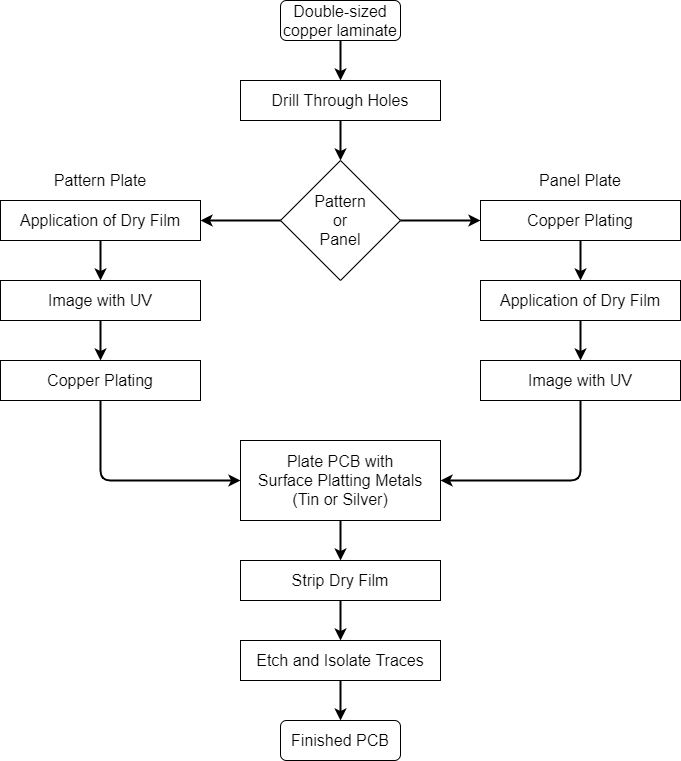
Figure 3 – PCB Assembly Process
PCBs first arose to solve the need for faster and more reliable construction of electric and electronic circuits, like the ones you see in your computer (the motherboard for example) and your washing machine.
Initially, PCBs were designed with Through-Hole-Technology in mind, meaning that individual components had to be inserted and soldered into the board itself. With time, a new idea emerged called Surface-Mount-Technology, which increased the speed of manufacturing and radically decreased the size of the final boards. These have come to dominate the PCB world, as they are more reliable, faster and cheaper to manufacture and are very flexible from the construction point of view, as they can be made into very specific shapes and sizes.
The process of manufacturing PCBs starts with a design, made by a team of electrical, electronic and mechanical engineers, which then gets printed on a copper plate. For a THT board, the copper laminate sheet is first drilled and then the actual traces are imprinted, coated and etched, resulting in the familiar green boards with lines and holes for the traces and components. SMT boards are similarly made, but do not require holes, as the components are soldered on the board on contact pads.
Advances and improvements have grown at a rapidly increasing speed in the last couple of decades, allowing us to now print not one, not two, not four, but up to thirty (30!) layers on one PCB. This allows for incredibly complex and intricate designs to be implemented, but also introduces multiple points of failure in the PCB, making troubleshooting and testing increasingly more difficult.
Cable Assembly
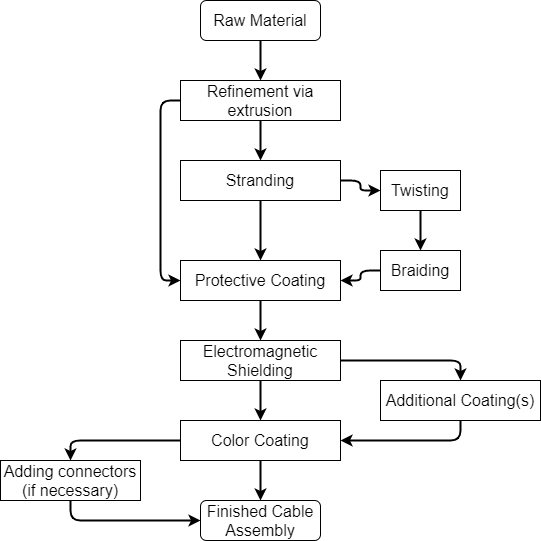
Figure 4 – Cable Assembly Manufacturing
Having a PCB is only a third of the problem, as you may need to connect multiple boards inside the same device or even multiple devices. For example, the internet is powered by cables connecting a huge number of computers together to form a distributed network, capable of transmitting cat photos, results of important research or encrypted memes.
Cable manufacturing is therefore an important part of electronics’ manufacturing, with the processes associated being fairly simple in nature.
First of all, a material, such as copper or fiberglass, is chosen to satisfy the requirements. Then the material is refined via extrusion, followed by stranding, twisting and braiding to get to the desired size, strength and other parameters that affect the use of it.
A bare cable is not able to withstand the elements on its own, so then comes the coating and layering step, which ensures the cable is water-proof, shielded from other electromagnetic fields, and fire-proof.
There are many types of cables, each with its uses, pros and cons. The most known are coaxial cable (used for transmitting radio and TV signals), ribbon cable (many wires bundled together, usually found in computers) and shielded cables (cables that have been wrapped inside a protective coating, to provide protection in high-voltage applications).
Electronic Packaging
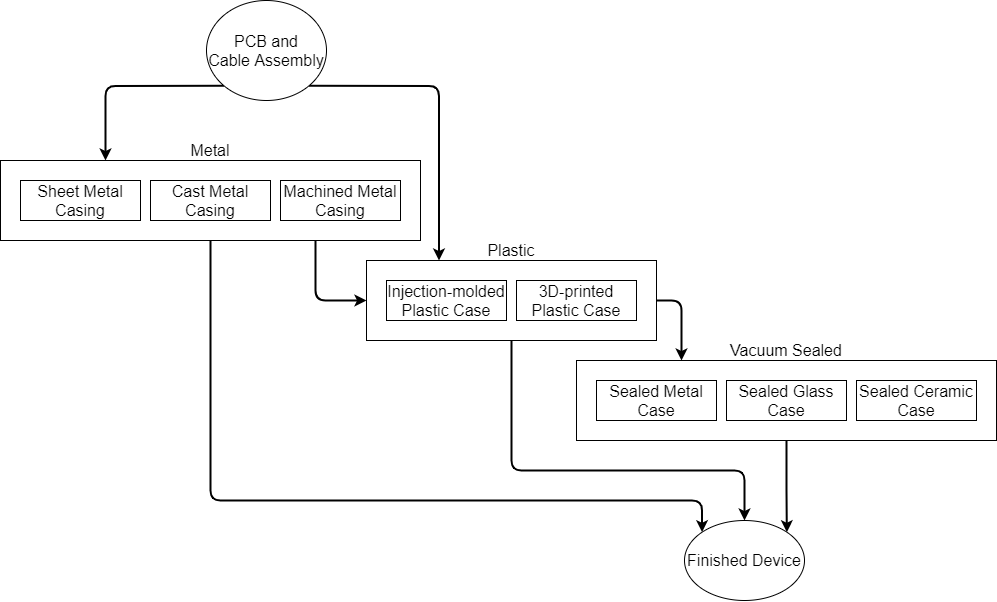
Figure 5 – Packaging Materials
Third, but not last, there’s the packaging of the device. This is rather straight-forward: pick the material according to the environment and exposure to the elements, create the enclosure, fix PCB inside the case, connect all cables to connectors on the surface of the case, seal (if necessary) the inside of the case from the outside with a protective film, coat or foam.
Although this may seem as a benign step, it is the most important step, as the finished device needs to withstand certain stresses and loads, so ensuring the actual package which contains it is up to spec is very important.
To name some of the packaging materials, we have sheet, cast or machined metals/alloys, moulded, extruded or injected plastic, plastic/resin coating, sealed metallic/ceramic/glass enclosures.
As part of enclosing a device, testing for certain criteria is necessary for reliability and warranty reasons. Well known is the IP certification, which ensures a certain degree of resistance to solid and liquid particles ingress: the first digit stands for solid particle protection and the second digit stands for liquid particle protection. There are also additional and supplemental letters, which are optional and have very specific use-cases.
Prototyping and Testing – Key Processes in Electronics Manufacturing
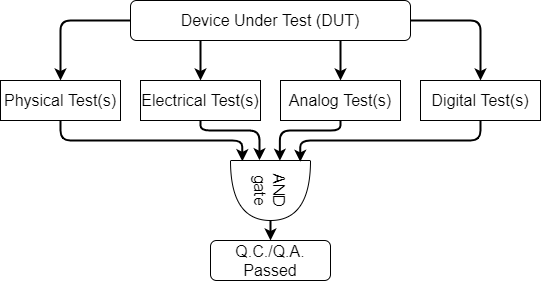
Figure 6 – Prototyping and Testing Processes
Lastly, there are the prototyping and testing processes, which are needed at the beginning and end of electronic manufacturing.
A prototype is similar to a first edition book. It is just a concept made real, so that you can test whether the idea is feasible or not, if the materials are able to perform as expected and find possible spots for improvements. This step is usually lengthy, arduous and consists of many labour-hours from engineers, which try to implement a new idea or technology, trying in the end to see if the resulting device can be mass-produced and at what cost.
On the other hand, testing comes last. After the electronic equipment has entered the mass-market production stage, testing is required to ensure the quality of the products; it is also known as quality control (Q.C.) or quality assurance (Q.A.), evidence of which can be found on any device in the form a sticker, stating the testing criteria that the device passed.
In most cases, testing comprises four major categories of tests: physical testing (seeing if a board can withstand certain amounts of heat), electrical testing (testing if electricity flows correctly through the board), analogue and/or digital testing (checking if the board works as intended, logic-wise). In the industry, the device being tested is referred to as DUT (Device Under Test), EUT (Equipment Under Test) or UUT (Unit Under Test).
Only if all tests are passed successfully can the manufacturer decide to move the board on to either large-scaled fabrication (if it was a prototype) or to the assembly line, where it gets put together with the required cables, connectors and case(s), and shipped to the client(s).
Current Trends and Future of Electronics Manufacturing
One aspect that is starting to gain more and more ground in recent years is the option for engineers and hobbyists to have their own designs produced in the same mass-market plants. This is known as ‘Made to order’ and is considered to be one of the possible trends, as decentralization and individual inventions are starting to make a rise again.
Another wave that is currently underway consists of electronics’ manufacturers helping new industries gain more traction, such as aerospace and space tourism, with the creation and refining of assembly lines which produce better and cheaper electronic components.
Lastly, but not to be ignored, is the rise of machine learning and artificial intelligence powered devices, which have the potential to revolutionize and change society as we know it. PCBs specifically designed for neural networks and machine learning algorithms have allowed artificial intelligence to truly shine and come out of the science-fiction world, with the most notable examples being GPT-3, Tesla’s upcoming Autopilot FSD suite and Deepmind.
FAQ
What do electronic manufacturers do?
Electronics manufacturing company designs, tests, manufactures, and distributes electronic products and assemblies for original equipment manufacturers.
What are Electronic Manufacturing Services?
Electronic Manufacturing Services, often referred to as simply EMS, are companies that offer to perform all the steps needed for the development and manufacturing of electronic products for original equipment manufacturers, or OEMs. Through these companies, OEMs can outsource some of their engineering and manufacturing tasks to improve their operational efficiency, reduce costs, increase speed and cut down on time to market, as well as focus on other central company activities such as research, development, strategy implementation, and marketing.
What is OEM in Manufacturing?
An original equipment manufacturer (OEM) is defined as a company whose products are used as components in the final products of another company.