IC test sockets, though often overlooked, play a crucial role in the semiconductor industry by facilitating the precise testing and validation of integrated circuits (ICs). Their development has paralleled the advancement of IC technology itself, transforming from simple devices to highly specialized tools essential for modern electronics.
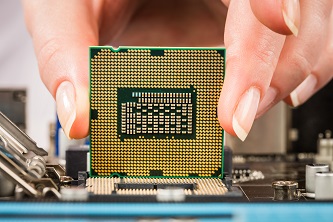
Understanding the various types of IC test sockets, from high-frequency and Kelvin contact sockets to tailored solutions for large BGA packages, is crucial for anyone involved in hardware testing and design. Each variation offers distinct advantages and capabilities tailored to specific testing needs, from power management to comprehensive engineering tests. Design considerations such as customization and material selection further underline the complexity and importance of choosing the right socket for the desired application.
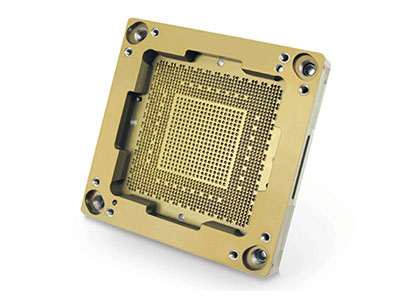
Photo credit: Smiths Interconnect
This guide delves into the nuances of IC test sockets, exploring their types, applications, and the innovations driving the industry forward. By examining the key players in the market and addressing the global demand for efficient and cost-effective solutions, we aim to provide an ultimate guide for professionals seeking to optimize their electronic testing processes. Join us as we navigate the challenges and advancements shaping the world of IC test sockets.
Overview of IC Test Sockets
IC test sockets are integral to the semiconductor manufacturing process, bridging the gap between a semiconductor device and a circuit board. Their design is crucial for testing the functionality and electrical performance of electronic devices. They enable a temporary connection, allowing manufacturers to conduct production testing without soldering chips directly onto boards. This temporary setup is vital for evaluating a wide range of electronic and electrical characteristics. IC test sockets must align precisely with semiconductor sockets to ensure accurate results. They are used in testing a variety of package types, enhancing the efficiency of semiconductor manufacturing processes.

Definition and Purpose
IC test sockets are devices that facilitate the testing of integrated circuits (ICs). These sockets temporarily connect semiconductor devices to circuit boards during testing phases. Their primary purpose is to ensure that chips meet performance requirements without causing damage. With a reliable contact system—often employing spring probe or Kelvin sockets—IC test sockets maintain a consistent connection. This minimizes signal loss and boost signal integrity. They are critical for evaluating the electrical characteristics of chips, assessing whether they meet the necessary standards. As such, they support the development of various electronic devices before mass production.
Historical Context and Evolution
The evolution of IC test sockets has paralleled advancements in semiconductor technology. In the early days, testing methods were rudimentary, often limited to static tests. As electronic devices became more sophisticated, the demand for efficient and reliable socket solutions grew. Historical developments saw a shift from basic designs to more complex solutions with Coaxial structures. These advancements have improved testing speeds and ensured more precise alignment of components. Over time, IC test sockets have adapted to accommodate a wide range of package types and signal paths. This evolution continues as new contact technologies emerge to meet growing industry needs.
Types of IC Test Sockets
IC test sockets are critical components in the semiconductor manufacturing process. They serve as the interface between the electronic device and the circuit board during testing. These sockets must meet various performance requirements, ensuring precise alignment and reliable contact. Different package types require unique socket solutions to maintain electrical characteristics. With advancements in semiconductor devices, the need for socket designs that support high performance and maintain signal integrity is growing. Let’s explore some common types of IC test sockets used in production testing.
High-Frequency Sockets for RF and 5G
High-frequency sockets are essential for testing RF and 5G semiconductor devices. These sockets are designed to manage the high speeds and precise requirements of modern communication technologies. The contact technologies used in these sockets help to reduce signal path disruptions, maintaining signal integrity. They often incorporate a coaxial structure to handle the complex signals associated with high-frequency operations. Ensuring that each connection maintains optimal electrical performance is crucial as it affects the overall functionality of RF and 5G systems. High-frequency sockets represent a key area of development, supporting the rapid advancement of wireless technologies.
Kelvin Contact Sockets
Kelvin contact sockets are designed for precise measurement applications. They use a dual-contact approach to provide more reliable connectivity. This design can measure electrical parameters like resistance with higher accuracy due to its reduced contact resistance. Kelvin sockets are often used in devices where precise electrical performance is important. They ensure that measurements meet strict specifications while reducing errors in signal integrity. As semiconductor devices grow more complex, the demand for Kelvin contact sockets continues to rise, underscoring their importance in ensuring accurate performance metrics.
Large BGA Package Sockets
Large Ball Grid Array (BGA) package sockets are used for devices with significant pin counts. These sockets need to accommodate the large size and specific pin arrangements of BGA packages. Their design ensures a reliable contact with each ball of the grid, which is critical for proper electronic communication. Large BGA sockets often use advanced spring probe technology to meet demanding production testing requirements. This allows them to provide the necessary contact force and alignment. They must also support a wide range of electrical characteristics, making them versatile solutions in semiconductor testing. With the ongoing advancements in technology, these sockets play a crucial role in supporting larger, more complex semiconductor packages.
Applications of IC Test Sockets
IC test sockets are essential tools in the semiconductor manufacturing process. They serve various roles, from research and development to production testing. These sockets help test electronic devices by providing a reliable contact to the integrated circuits (ICs). This allows engineers to evaluate electrical characteristics and other performance requirements. With their precise alignment and varied socket designs, these tools ensure seamless integration with circuit boards. They cater to a wide range of semiconductor devices, enhancing efficiency and accuracy. They also offer custom socket solutions to meet specific needs in semiconductor testing, making them a critical component in the field.
Power Management Testing
Power management testing is crucial for ensuring that semiconductor devices operate efficiently. IC test sockets play a vital role in this process by allowing precise testing of power management circuits. These sockets provide a dependable signal path, which helps engineers analyze signal integrity and electrical performance. Through the use of advanced contact technologies, IC test sockets ensure reliable contact during testing. This phase often involves testing different package types to confirm that they meet set electrical requirements. By supporting various socket designs and Kelvin sockets, these test sockets help measure voltage levels and current flow accurately.
Engineering Tests
Engineering tests form a fundamental part of semiconductor development. IC test sockets are key in conducting these tests by providing a custom fit for each semiconductor device. They are designed to meet specific engineering challenges and performance requirements. During these tests, a socket product must support complex ICs while maintaining signal integrity. The sockets also enable thermal and burn-in testing to evaluate durability under extreme conditions. With features like coaxial structure and spring probes, these sockets ensure accurate results. They help engineers analyze electrical and mechanical properties, which assists in optimizing device design and performance.
Design Considerations
When designing IC test sockets, several factors need careful attention. These sockets are crucial for ensuring that semiconductor devices meet performance requirements. A well-designed socket can enhance electrical characteristics and provide precise alignment for semiconductor manufacturing processes. It should cater to a wide range of package types and maintain signal integrity. Designers must also consider the socket’s electrical performance and reliable contact with electronic devices. Meeting these standards ensures efficient production testing and high-quality semiconductor device outputs. Each choice in the design process affects the final SOCKET PRODUCT’s functionality.
Customization Options
Customization of IC test sockets allows for tailored solutions to meet specific needs in semiconductor testing. Designers can adjust socket metrics like contact technologies, spring probe styles, and electrical characteristics. They may also implement Kelvin Sockets for improved accuracy in measurements. Socket solutions can be designed for different package types, ensuring optimal performance for each unique application. Custom solutions can also enhance signal path efficiency and signal integrity. This flexibility is crucial for adapting to the fast-paced demands of the semiconductor industry and maintaining a competitive edge.
Material Selection
Selecting the right materials for IC test sockets is crucial for their effective functioning. Materials impact the socket’s durability, conductivity, and overall performance. When choosing materials, consider factors like electrical conductivity, heat resistance, and mechanical strength. The right material ensures reliable contact and supports the socket’s performance in various conditions. In addition, using high-quality materials can improve the semiconductor test socket’s life span. Therefore, careful material selection is essential for maintaining reliable contacts and meeting the stringent demands of electronic devices and circuit boards. A failure in this step can lead to compromised test results and increased failure rates in the final SOCKET PRODUCT.
Innovations in IC Test Sockets
IC test sockets play a pivotal role in semiconductor manufacturing. Their main function is to test integrated circuits (ICs) by providing reliable contact between the device and the test equipment. As technology advances, so does the need for more sophisticated socket solutions. These sockets must cater to various package types and meet stringent performance requirements. With innovations continually emerging, engineers strive to enhance signal integrity and electrical performance. The quest for efficient socket design is driven by the need to maintain precise alignment and adapt to a wide range of semiconductor devices.
Recent Trends in the Industry
The IC test socket industry is evolving with new technologies and materials. Contact technologies are improving, with burn-in sockets now available in materials that offer better durability and electrical characteristics. The move toward miniaturization in electronic devices also demands sockets that can handle smaller, more intricate designs. Innovations like Kelvin Sockets are becoming popular for their precise measurement capabilities, crucial for maintaining semiconductor electrical performance. Additionally, the adoption of sockets with a coaxial structure enhances signal integrity, making them more efficient in high-frequency applications.
Role of Precision Engineering
Precision engineering is vital in the design and production of IC test sockets. This discipline ensures that each socket meets the specific needs of different semiconductor devices. The engineering process takes into account the unique signal path each socket must accommodate, ensuring reliable contact and optimal performance. For instance, the use of spring probes in socket design helps maintain electrical contact even under varying pressures. Precision engineering also considers socket alignment to provide a reliable connection and support a seamless semiconductor manufacturing process. This attention to detail is crucial for meeting the demands of modern circuit boards.
Key Players in the Market
The IC test socket market boasts several key players who excel in providing innovative socket solutions. These companies focus on ensuring reliable contact technologies and optimal electrical performance for semiconductor devices. They cater to a wide range of package types in the semiconductor manufacturing process. By achieving precise alignment and understanding electronic device requirements, these players contribute to the success of production testing and semiconductor test socket design. Their expertise supports signal path integrity and meets the varying performance requirements of circuit boards. Here, we will explore two notable companies making significant strides in this industry.
Global Industry Reach
IC test sockets play a crucial role in the semiconductor industry worldwide. These small yet vital components ensure reliable electrical connections within electronic devices. As semiconductor technology advances, the demand for sockets is growing. This is because new devices need efficient testing solutions. IC test sockets are essential for global electronics manufacturers. They help ensure product quality and performance. They are used in various applications, from consumer electronics to industrial machinery.
Companies must consider international market trends and local regulations. This allows them to meet diverse needs and tap into new opportunities. By offering a wide range of socket solutions, businesses can cater to different package types and performance requirements. In this global market, flexibility and adaptability are keys to success. A deep understanding of socket design and semiconductor manufacturing processes helps companies thrive.
Demands for High-Performance Solutions
In today’s fast-paced world, high-performance solutions are in demand more than ever. IC test sockets are no exception. These sockets must meet stringent performance and electrical characteristics. Precise alignment and reliable contact are paramount for effective testing. The semiconductor industry relies heavily on sockets for production testing and development.
Innovations like Kelvin sockets and spring probes are gaining attention. They help ensure accurate results and optimal electrical performance. Meanwhile, technologies like Coaxial structures improve signal integrity. These advancements support the industry’s needs in both performance and precision. As technology evolves, so do the demands for better and faster socket solutions.
High-performance solutions require intricate designs and attention to detail. For companies in the semiconductor test socket market, meeting these demands is both a challenge and an opportunity. By focusing on cutting-edge technologies, firms can excel in this competitive landscape.
Cost-Effective Approaches
With rising production costs, finding cost-effective approaches is critical. IC test sockets must balance price with performance. Companies are exploring new ways to reduce expenses while maintaining quality. One strategy is developing custom solutions tailored to specific needs.
Many manufacturers opt for burn-in sockets due to their affordability. Such sockets are essential for testing during mass production. They are built to withstand extended testing periods, thus reducing replacement costs. Additionally, innovative contact technologies help decrease maintenance needs.
Gravity feed designs also provide cost-saving advantages. These designs streamline assembly and reduce labor requirements. By utilizing efficient manufacturing methods, companies can minimize expenses without sacrificing performance. Addressing the cost factor is vital. It ensures competitiveness and enhances the value of socket products.
Challenges and Solutions
IC test sockets are crucial in the testing of electronic devices. They help evaluate the performance of circuit boards and semiconductor devices. However, these sockets face several challenges due to varying semiconductor manufacturing processes and package types. Each socket must meet specific performance requirements and electrical characteristics. To overcome these issues, socket solutions must be precise and adaptable. Reliable contact technologies are essential to ensure that the sockets perform under different conditions. Advanced designs like Kelvin Sockets and Coaxial structures enhance signal integrity. They work effectively across a wide range of applications. By focusing on accurate alignment and signal paths, these sockets help in maintaining signal integrity throughout testing.
Addressing Testing Limitations
IC test sockets must work seamlessly with various semiconductor devices and circuit boards. The wide range of package types and designs presents a challenge. Semiconductor test sockets need to adapt to different design and performance requirements. Gravity Feed and Land Grid Array are just some examples. Socket design must accommodate diverse setups. This ensures reliable contact and optimal electrical performance. Contact technologies are crucial. They provide the necessary connection strength. Spring probes are often used. They help achieve this reliable contact during testing. By handling these factors, IC test sockets can address testing limitations efficiently.
Ensuring Durability and Accuracy
Durability and accuracy are vital for the IC test socket’s performance. These sockets must endure extended use in production testing. Socket solutions must be robust to maintain consistent electrical performance. This involves choosing materials that withstand repeated testing cycles. Additionally, precise alignment during testing is necessary. It ensures that electronic devices are evaluated accurately. Achieving this involves custom solutions tailored to specific needs. Semiconductor sockets also focus on electrical characteristics. They must maintain signal integrity without interference. By enhancing these aspects, reliability is ensured throughout the testing process. Technology advancements continue to improve the durability and accuracy of these sockets.
IC Test Socket Price Overview
IC test sockets are vital for testing electronic devices before they hit the market. They ensure reliable contact with circuit boards during the production testing process. The price of an IC test socket varies based on several factors, such as package types, design complexity, and performance requirements.
Here’s a quick overview of typical price ranges for various package types:
Land Grid Array (LGA): $50 – $150
Ball Grid Array (BGA): $100 – $300
QFN/DFN: $30 – $100
DIP/SIP: $20 – $80
Factors affecting price include the need for precise alignment, the electrical characteristics desired, and any custom socket solutions. Kelvin sockets, known for high electrical performance, might cost more due to their advanced contact technologies.
For specific semiconductor device testing, a custom socket design might be necessary, leading to higher costs. However, investing in quality socket solutions ensures signal integrity and reliable contact, essential for the semiconductor manufacturing process.